This article will reveal some of the internal insights that we have gathered since doing digital twin simulations with the UR20. As most of us know, this robot is larger than its predecessors. Therefore, it is essential to be aware of certain factors when considering its use for palletizing tasks.
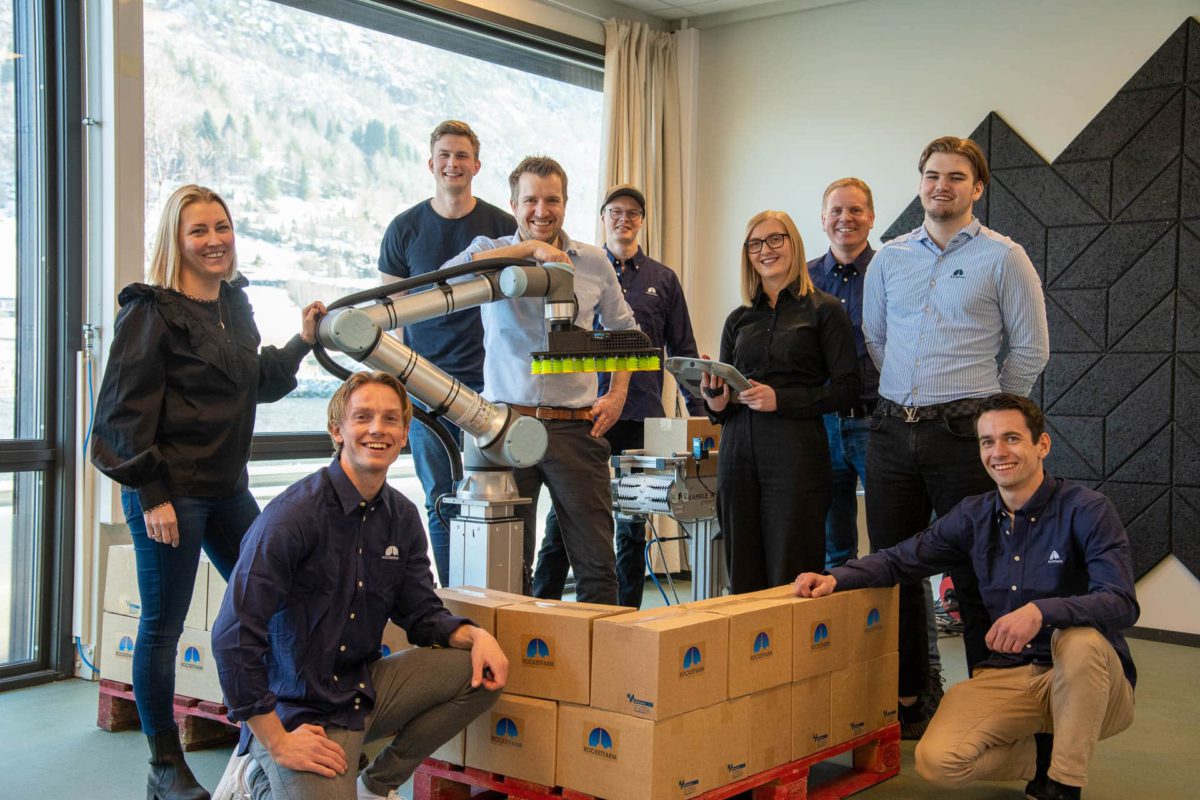
The latest addition to the cobot family from Universal Robots has got many companies excited. They are curious about its ability to handle industrial applications and how well it can perform its tasks.
Within the palletizing segment, we are gathering valuable insights about what the UR20 can and cannot do through our simulations. These simulations are necessary to know the possibilities and challenges when using the new cobot for palletizing.
We do digital twin simulations through the MyRobot.cloud platform. The platform enables sales engineers to verify and engineer cobot palletizing projects with digital twin simulations.
Try MyRobot.cloud 30-days for free.
More efficiency with higher payload
If you compare the UR10e with the new UR20, you’ll surely notice a significant difference. We have already done digital twin simulations that inform us about some of its significance.
With products weighing 6 kg, the UR10e could pick one box per cycle due to payload limitations. In contrast, the UR20 would double-pick and palletize the same products more efficiently.
And the results? With the same hardware and software configurations, the cases-per-minute (CPM) increased from 7,01 to 11,47. In this example, the average time per pallet went from 13 minutes and 42 seconds to 8 minutes and 22 seconds.
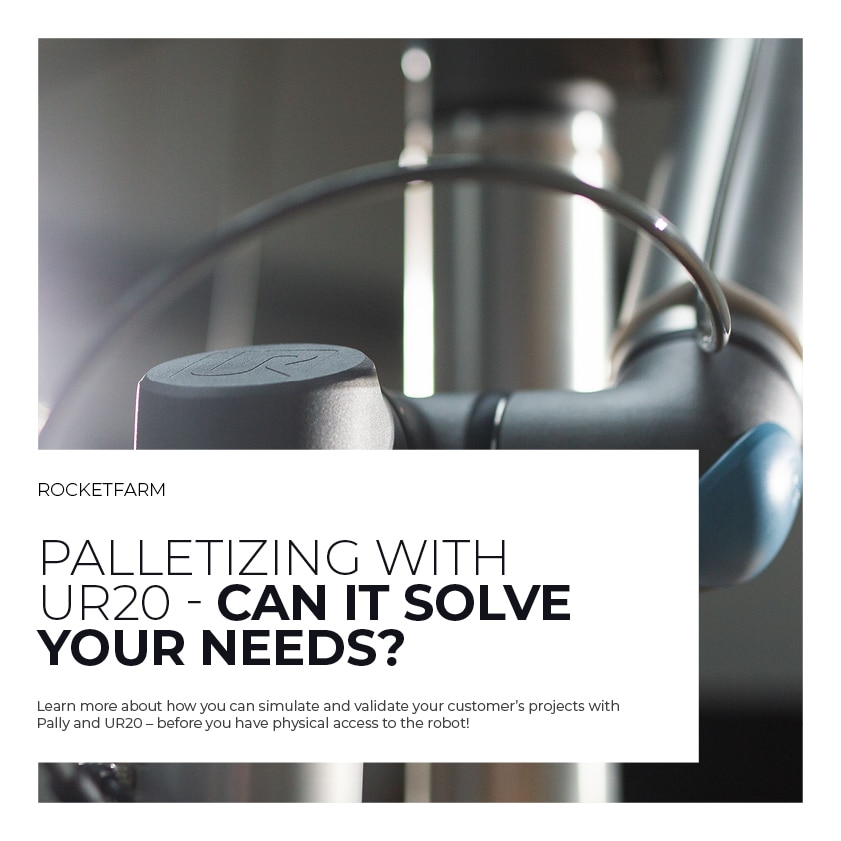
Keep reading or download our free UR20 Ebook to learn more
Increase safety settings while meeting CPM requirements
In general, the outcome of enabling double- or multi-pick is not only about the possibility of more efficient palletizing. It’s also about safety.
With the UR20, more flexibility exists to increase such safety settings and still reach the desired CPM requirement. For projects that utilize the higher payload capacity by double picking, it’s possible to further restrict the max speed by half. By doing this, the palletizing cell is safer for workers close to the operating cobot.
Increased cobot lifetime
You can still meet the case-per-minute requirement with higher payload capacity, enabling double pick and restricting operational speeds. In sum, this will reduce what we call “wear and tear”, ultimately increasing the cobot’s total lifetime.
Due to its higher payload and extended reach, the UR20 makes cobot palletizing available to many manufacturers. We’ve seen a high demand for palletizing solutions in this payload range.
Egil Mundal
CEO, Rocketfarm
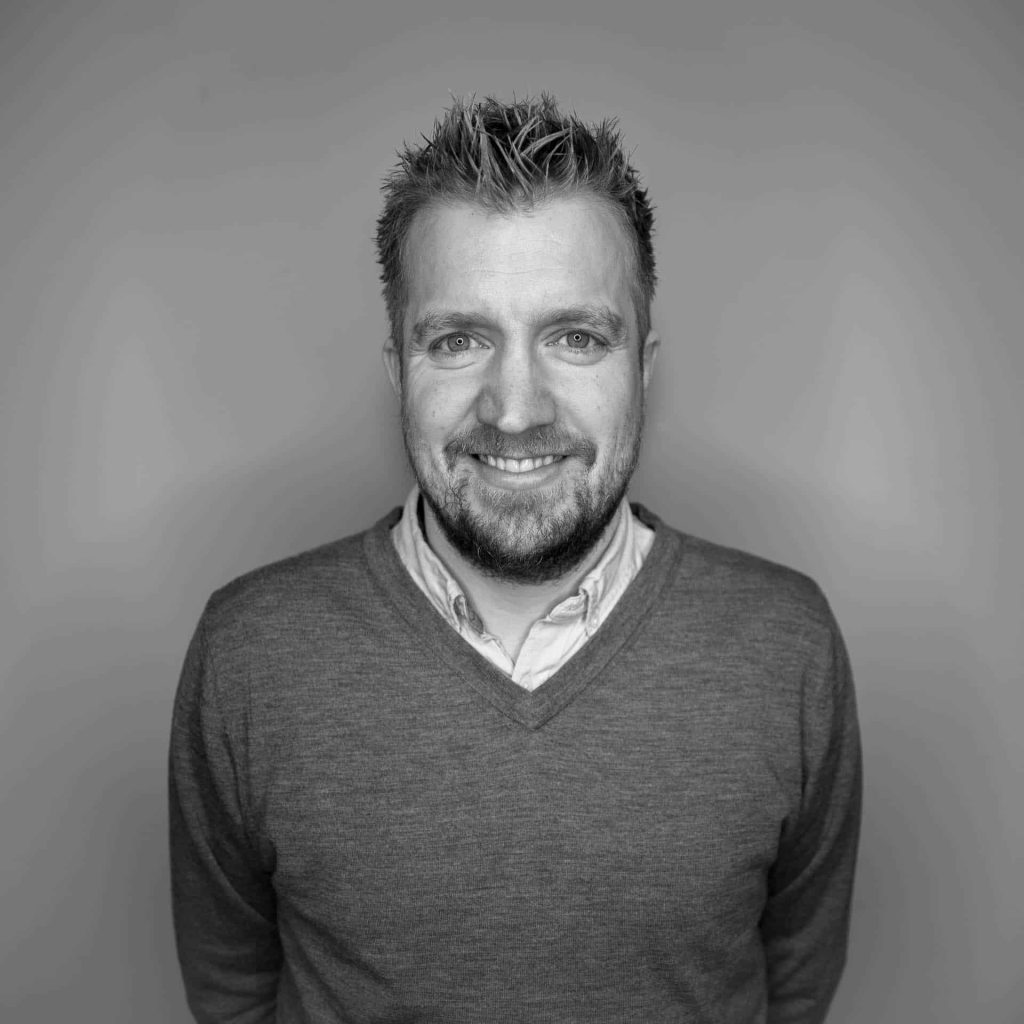
Less need for extra hardware
Depending on the box size, the UR20 can palletize at least 2 meters in height with a fixed mounting height (learn more about the best mounting height further down the article). When you start palletizing higher than 2meters, it starts getting complicated.
We have proven that a UR20 with Pally can palletize 2.45m without lifting column, but this is very dependant on both product size and pattern.
What we have learned from our digital twin simulations with UR20 is that if you plan to palletize higher than 2m, we will recommend to include a lifting column in the solution. This will give you more flexibility in terms of new products/patterns, more efficient palletizing and less need for advanced engineering to solve potential reach issues.
In comparison, the UR10e can palletize between 1,4, and 1,6 meters with a fixed piedestal. For some manufacturers, this is too low for what they would like. As a result, for palletizing solutions with UR10e it has been necessary to include a lifting column in the solution to meet the customer requirements.
Including additional hardware is always a trade off as it can also contributes to the overall complexity of the palletizing solution, which can lead to increased downtime for repairs and malfunctions.
But conclusion from our side is that if you are to palletize above 2m you are better off with a lifting column.
No pallet issue
In our experience, there have been some challenges with the UR10e when applying projects with bigger pallets.
However, the UR20 has a better reach, which allows it to palletize on any pallet, including US1, AU1, and CHEP pallets. It can easily reach the farthest locations on the pallet without any issues.
The image shows a screenshot of a simulation done with the large CHEP 1200X1200 mm pallet.
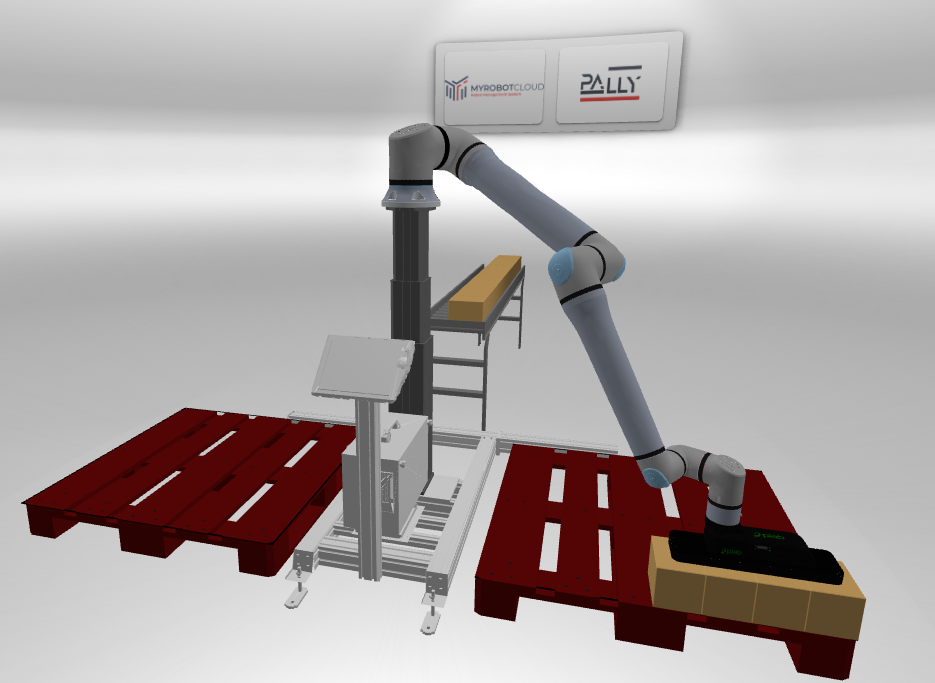
Pallet distance
For palletizing with the UR10e, the distance between the pallets in a palletizing cell has been 660 mm. However, with a bigger robot like the UR20, you need more space between the pallets.
We observed the robot arm accidentally hitting boxes on the pallet stack during our simulations – meaning that in a real-life scenario, the cobot would collide with the boxes and halt its palletizing process.
The issue relates to the distance between pallets and the larger size of the cobot.
We suggest placing the pallets in the palletizing cell with a space of 800 to 900 mm between them to address this issue. This way, you’ll avoid the clipping problems, as shown in the examples below. This clipping issue is related to the cobot’s bigger “elbow” and the “shoulder” too.
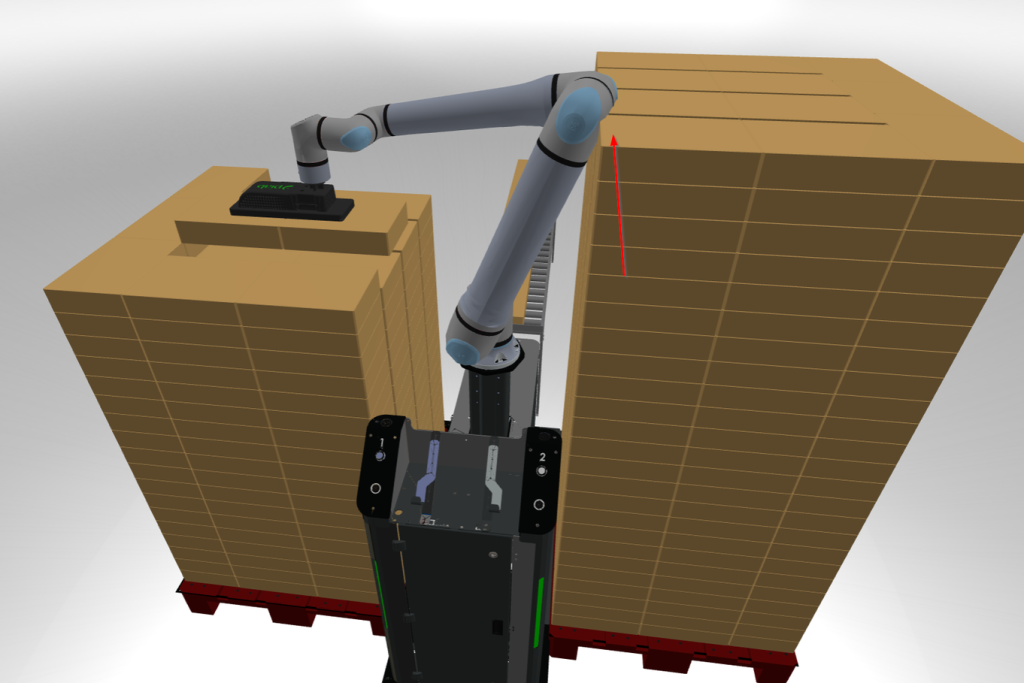
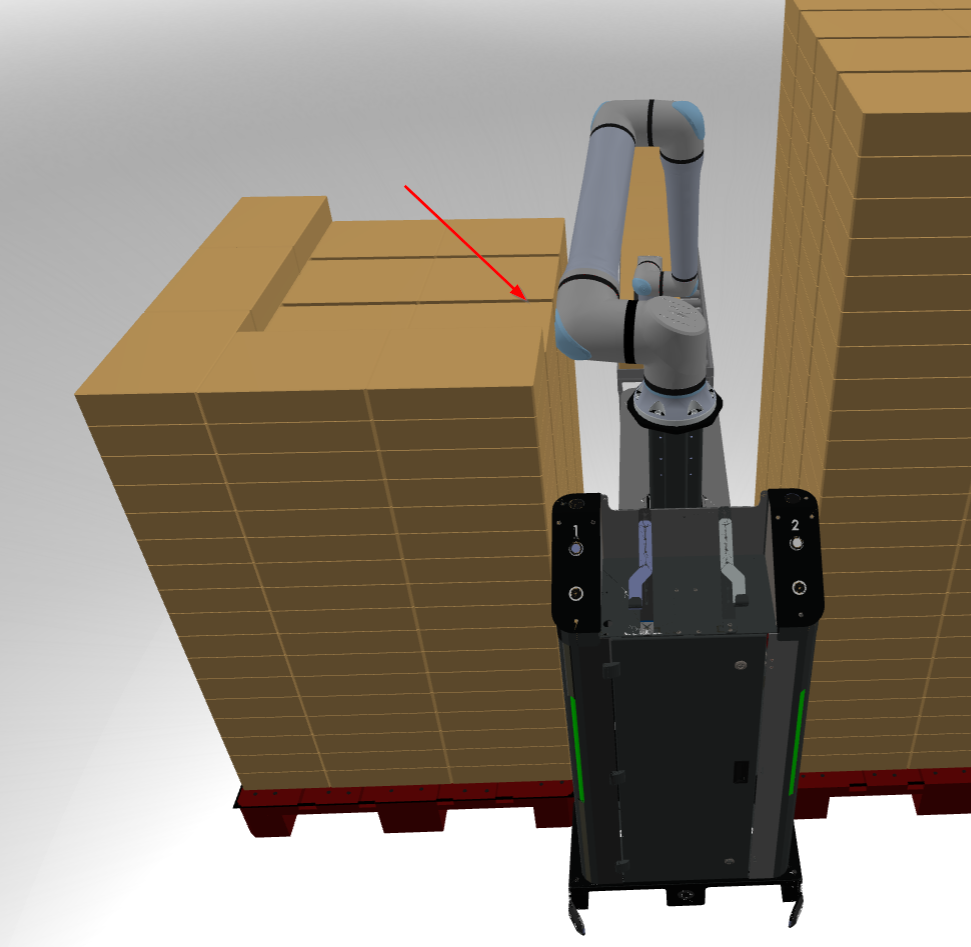
Cobot height
The previously mentioned insight is related to the horizontal axis of the cobot’s movements. The following insight discusses the difficulties associated with moving vertically.
With a mounting height of about 1300mm, the cobot can palletize all patterns below 2 meters. In our experience, this is also sufficient for many of our end customers.
Even though the new UR20 has 450 mm more reach than the UR10e, it does not mean that lifting columns will be of no use any longer. Some like to have the flexibility of palletizing above 2 meters.
In our example simulation below, “elbow “clipping is visible when placing boxes in the top layers above 2 meters. A lifting column is then needed to avoid a collision like this.
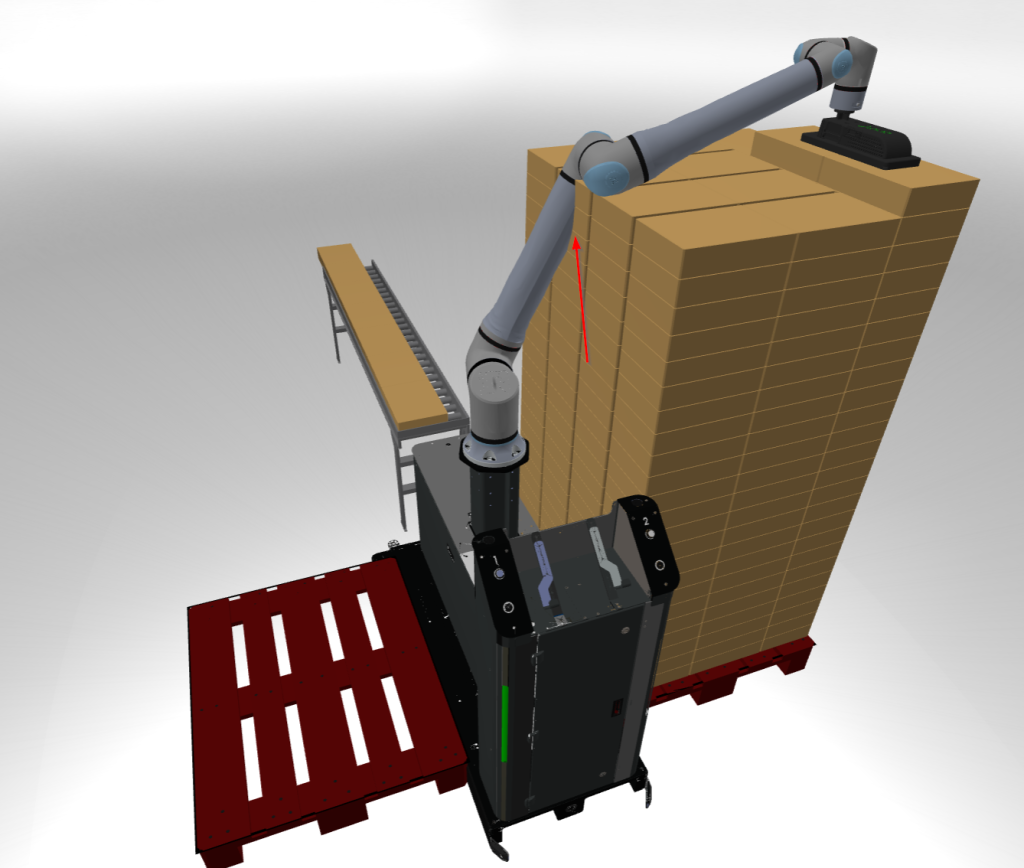
Grip quality and palletizing speed
Grip quality and the effect it has on the speed of palletizing is something rarely discussed. It has been less relevant with the UR10e where payload is relatively low. With the UR20 grip quality and it’s effect on palletizing speed is a parameter to be aware of.
Important to know: Without adjusting smart acceleration it will be almost impossible to reach 7-8 cpm with UR20 when single picking big boxes.
In Pally grip quality is automatically calculated. When palletizing bigger boxes (can be both big single box or multiple boxes) , speed will be reduced to ensure that the gripper maintains a good grip of the boxes during handling.
In Pally this is controlled by Smart Accelaration. Per default this is set to Medium. There are 5 different settings ranging from slowest to fastest.
In our experiment we where able to improve the CPM fra 6.5 to 11.75, just by adjusting the smart acceleration from medium to fastest. If you’re struggling to reach that hard to get CPM, this might be a setting to adjust and simulate one more time.
Conclusion
By using digital twin simulations to test multiple different settings in multiple different scenarios we have been able to learn a lot about what is possible and what is not possible with the UR20 in palletizing. The UR20 is a palletizing robot per se and holds great potential to enable automated palletizing for manufacturers around the world.
But you also need to know your robot, your software and how to unlock the potential.
With Pally and MyRobot.cloud you can also get the best out of the UR20.
We hope that we have been able to shed some light on the potential of UR20 for palletizing. If you would like to offer a UR20 palletizer to your customers, please contact us.
Sign up for our newsletter and get a FREE ebook
By signing up for our monthly newsletter, you’ll get case stories, product launches, and tips to automate your production line!
Additionally, you will instantly receive an ebook about implementing palletizing. For more information, please visit our newsletter subscription page.
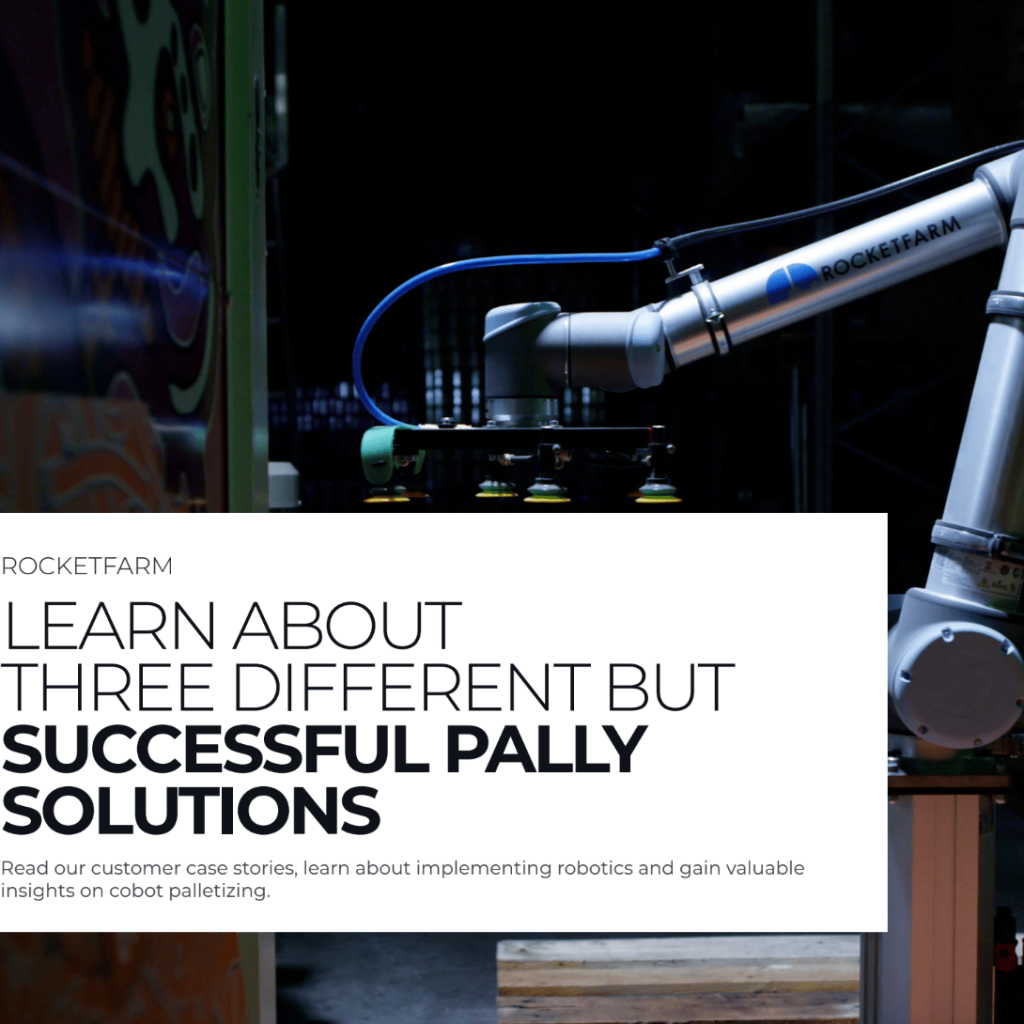