In this article, we will cover the topic of safety in palletizing solutions.
By the end of this article, you should know more about collision force, how to test different safety settings, and what settings you can change to make your solution safer.
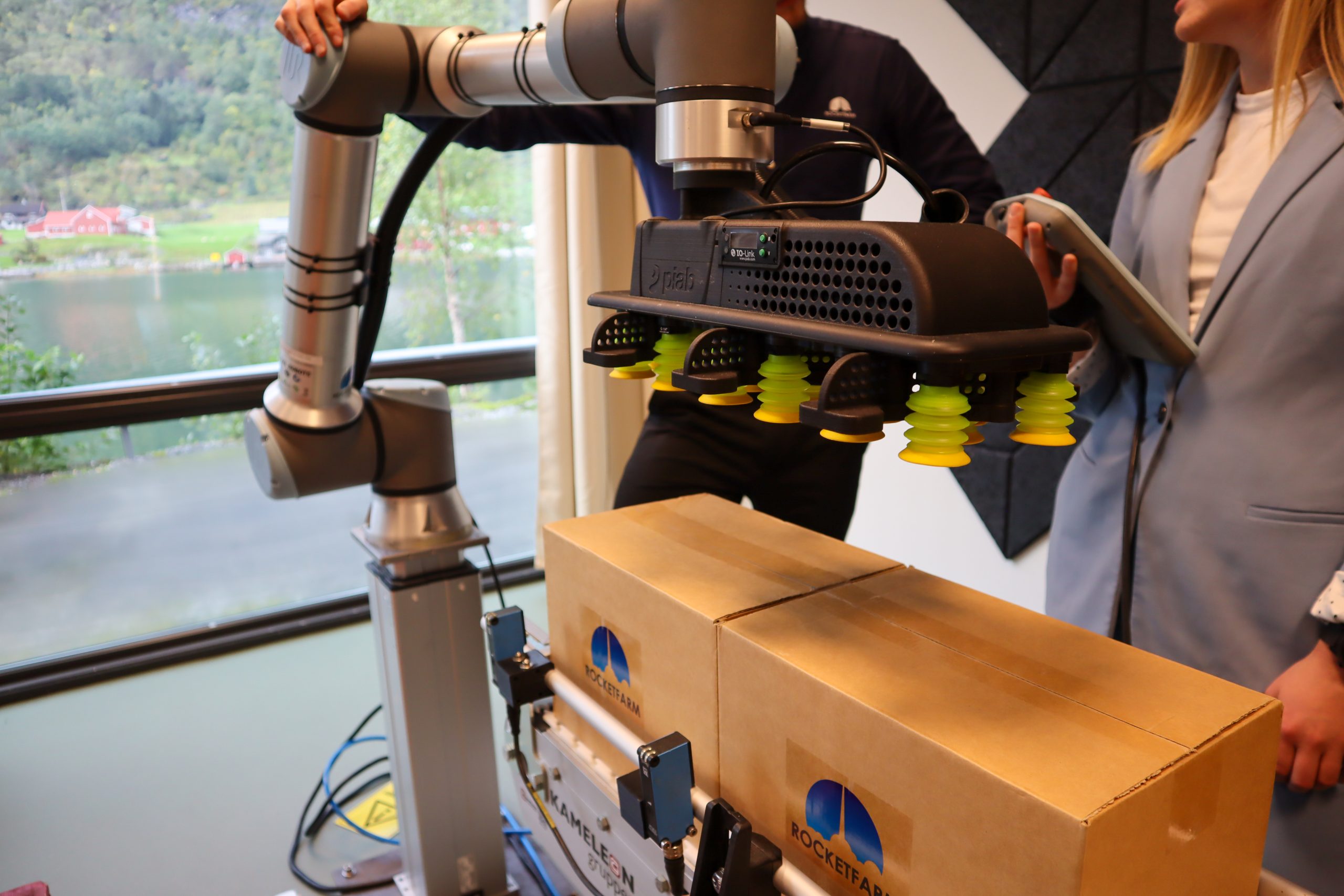
Below you’ll see a video of two similar palletizing solutions. They both use the same hardware but have different software settings. Interestingly, the robot on the left, which palletizes the fastest, is also the safest.
During palletization, the left one palletizes faster but only moves at half the maximum speed (the left is 756 mm/s, and the right is 1340 mm/s). Having a difference in speed makes a big difference in assessing solution safety, which you can learn more about below. The left robot compensates by accelerating faster and completing more picks per minute than the other.
Speed is vital
As cobots are programmed to stop if they hit a person, the main factor of the danger posed by a cobot is not the force which it can push a person towards a barrier, but rather the collision energy of the system.
Therefore, the collision energy of an impact is crucial in assessing the level of hazard in a cobot application. The equation that simplifies the “ISO 15066 Robots and robotic devices — Collaborative robots” is E=1/2mv^2, where speed (v) plays a significant role.
In fact, speed is the key factor in this scenario. It may not seem like it at first, but the speed of the system is what matters the most. The interesting part is that extra payload can be transferred to slower speeds, resulting in significantly lower collision energy.
Safer palletizing through adjustable software settings
Software settings play a crucial role in ensuring the safety of collaborative robots used in palletizing solutions. And from our point of view, software settings are often underestimated.
Cobots are designed to work alongside humans and share the workspace, which means they must be programmed to operate at a safe speed that does not pose a risk to human operators.
Palletizing solutions can be safer and more efficient by testing different software settings to control the robot’s movements. By adjusting the speed settings, the robot’s movements can slow down to reduce the risk of injury if it collides with a person or an object. For several reasons, it’s ideal to make the robot move as slowly as possible while still meeting production requirements, e.g., wear and tear, safety, and power usage.
Would this also be relevant for UR20?
The UR20 palletizer is suitable for a wide range of palletizing applications since it has a payload capacity of 20 kg. Compared to the UR10, It has an extended range and increased lifting capacity, but keep in mind that this will also result in a significant increase in moving mass.
For comparison, the UR10 weighs in at about 29 kg and can carry a payload of up to 12.5 kg with Pally, and the UR20 weighs in at about 64 kg and can carry a load of up to 20 kg. Let’s do the same calculations as we did above but for the UR20 with a 20 kg payload. This brings us to a total weight of 84 kg.
In the UR20, the kinetic energy is approximately 75.3 joules at a maximum speed of 1340 mm/s, and approximately 24 joules if the software settings are changed to 756 mm/s. In other words, testing different software settings can significantly impact the safety of your palletizing solution.
Perspective
The UR20 is more prominent and bulkier than its predecessor but should not be ignored in “lighter” production lines (6,5–10 kilos per box).
While the UR10 remains a viable option for most production lines, the UR20’s enhanced payload capacity and customizable software settings make it a safer choice for heavier applications. To reach a given CPM requirement, the UR10 would need to pick one box at a time at a certain speed, while the UR20 could utilize the multi-pick function in Pally at a slower pace, providing a safer alternative.
Learn more about palletizing with UR20 here.
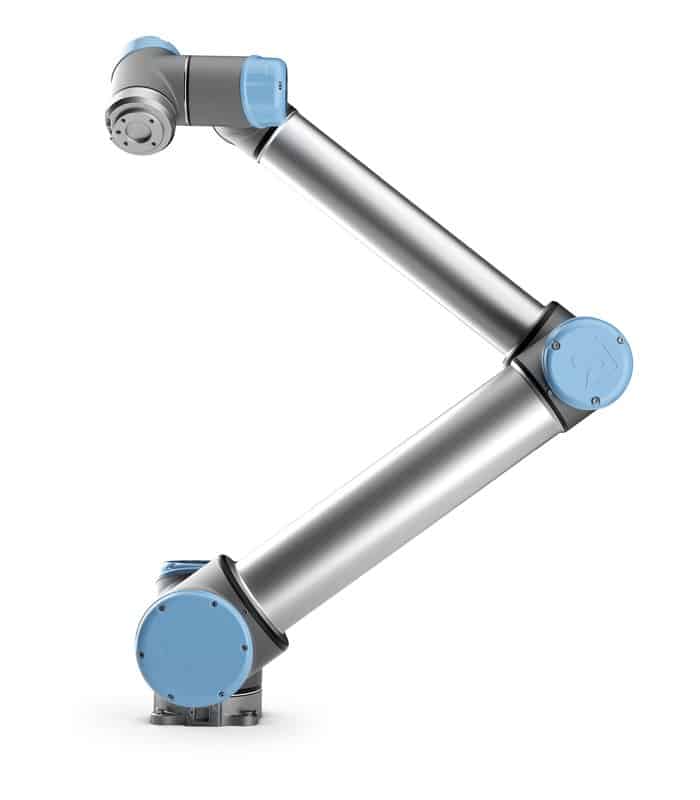
Enhance safety and increase productivity through MyRobot.Cloud
MyRobot.cloud is a robot management platform that allows you to do a lot of different things. Relevant for this article is that it enables you to optimize palletizing solution safety and productivity by testing different hardware and different safety settings for the same solution and pattern.
Want to try it? Request access here
From the example above, the robot on the left has managed to lower the collision force and increase the number of boxes picked per cycle by increasing the acceleration speed. Testing this physically would take hours if not days. Testing it in MyRobot.cloud will only take minutes of your time.
How to test acceleration speed in MyRobot.cloud
After you have gained access to MyRobot.Cloud, you can follow the steps in the video below using safety presets and customizable speed settings.
The results can then be further analyzed by comparing multiple simulations with different software settings.
Learn more about MyRobot.cloud in our knowledge base or contact us for a detailed explanation.
Sign up for our newsletter and get a FREE ebook
By signing up for our monthly newsletter, you’ll get case stories, product launches, and tips to automate your production line!
Additionally, you will instantly receive an ebook about implementing palletizing. For more information, please visit our newsletter subscription page.
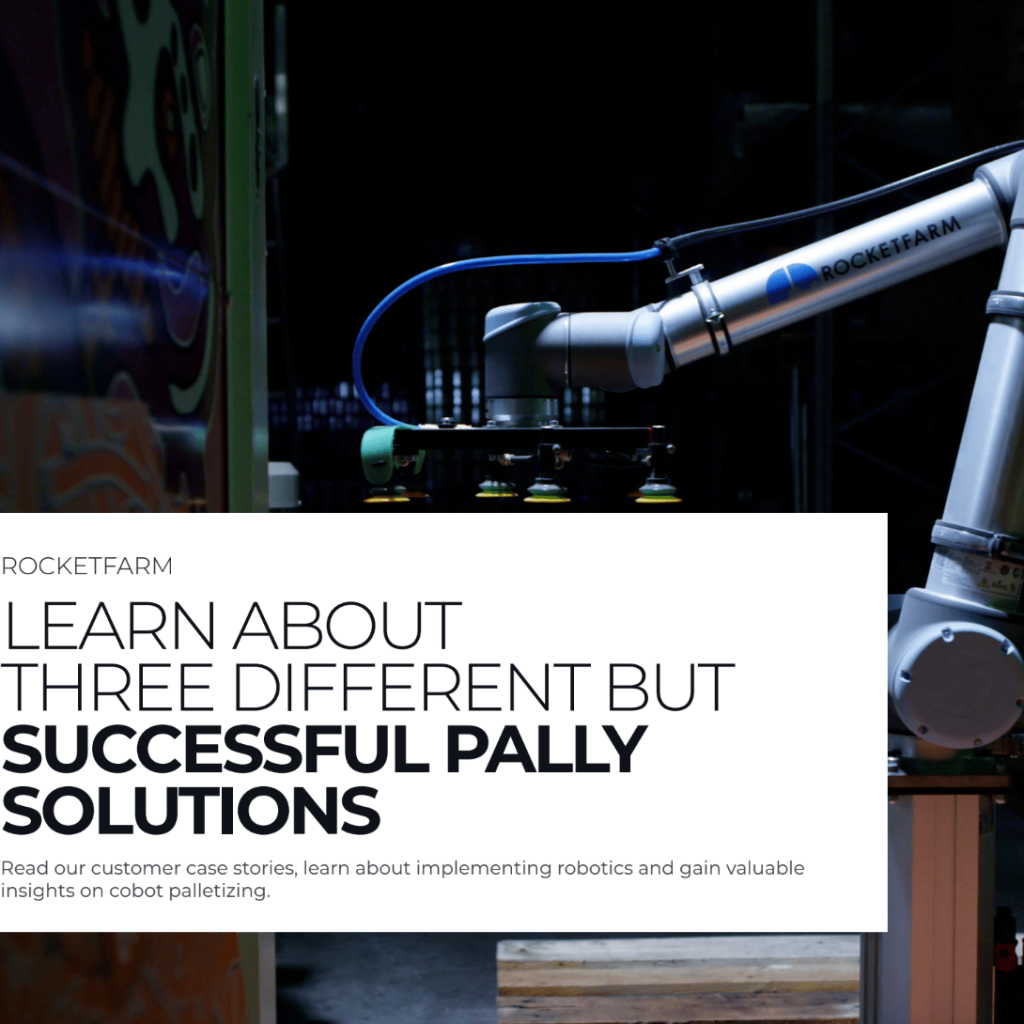