The rise of cobots and increasingly intelligent robots has created a new dilemma for organizations seeking to join Industry 4.0.
This article offers a deeper understanding of the differences between a cobot palletizer and a robot palletizer, presenting the advantages and disadvantages of both solutions, so you can make well-informed choices before deciding on a cobot or a robot for your specific needs.
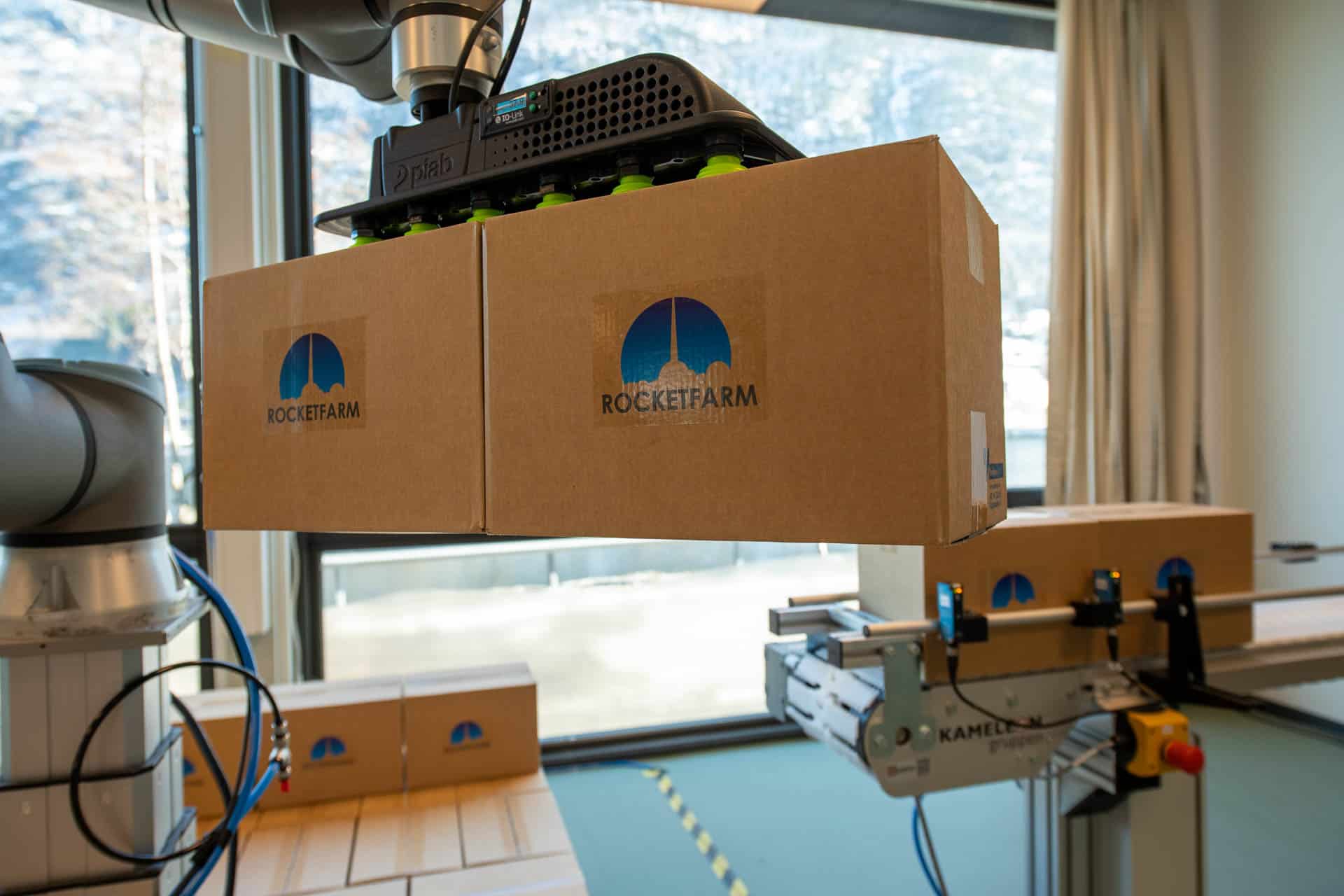
Cobot vs Robot Palletizer, what is the difference?
First things first, what defines a cobot and what defines a robot? Let’s dive deeper into each of them.
Cobots
The expression “Cobot” is short for collaborative robot, referring to a robot designed to work in collaboration with humans.
The cobot is required to operate within certain parameters to be permitted to work in the same area as humans: maximum speed, safety measures, and human supervision. This means that a cobot is limited to operations where the speed of the conveyor or production does not exceed the speed of the cobot. They are well-suited for tasks where humans work closely or even alongside the conveyor, such as pick and place, polishing, grinding, and machine tending tasks.
Short and Easy Installation Time
Some advantages of a cobot are the short installation time, easy interface, and flexibility. A complete cobot palletizing solution can be installed in a matter of weeks, encompassing everything from validation and fabrication to installation.
This case story is an example of how quickly it can be done.
Smaller and More Agile
In addition to the short installation time, the cobots provide a more straightforward interface that requires minimal training to use and program.
Software like Rocketfarm’s Pally makes it easy to modify and adjust your cobot. Compared to an industrial robot, a cobot is often much smaller in size, can be installed in various places, can perform multiple tasks, and does not necessarily require fencing or major area adjustments to ensure safety. Combined with easy programming makes the cobot a lot more flexible than an industrial robot.
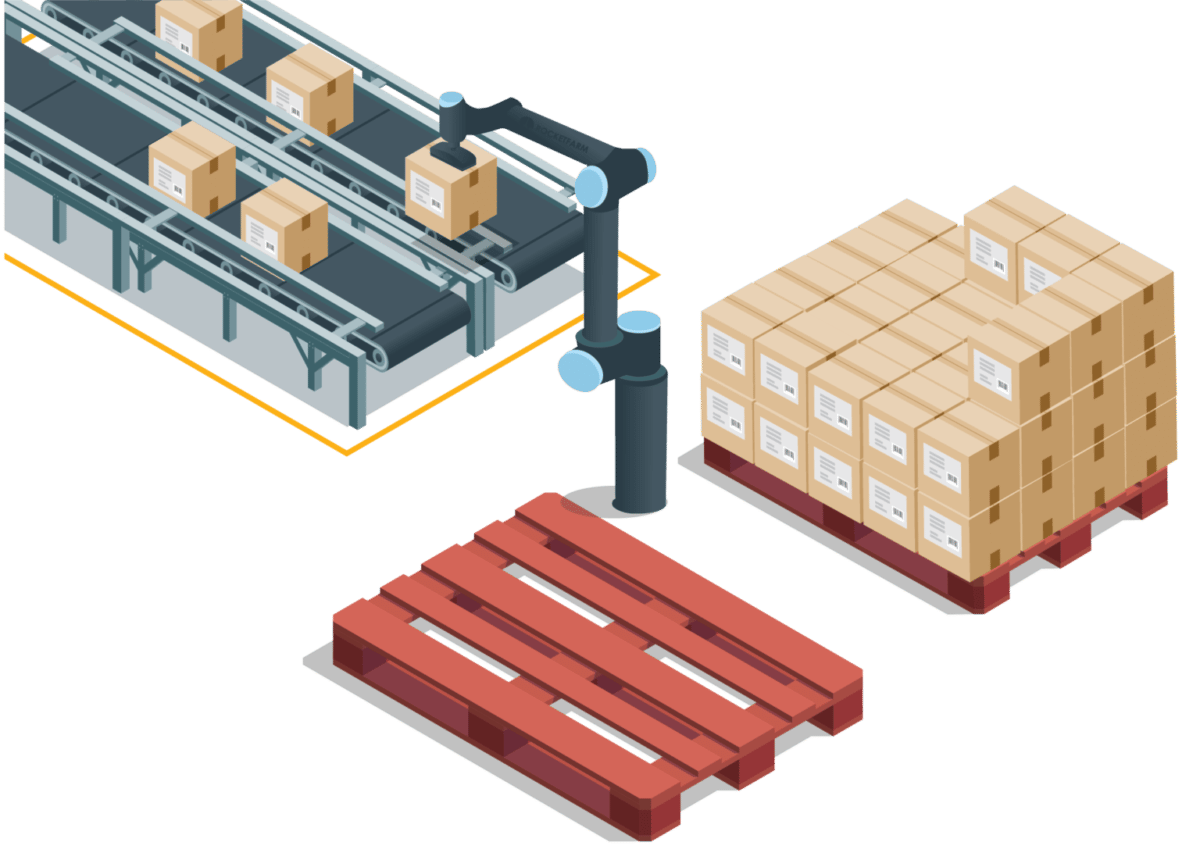
Robots (Industrial Robots)
A robot is not bound by the same parameters as a cobot, such as speed limitations, because it usually requires a cage. Automation with a robot requires a “fixed workcell” to operate safely, which necessitates a more comprehensive installation process and increased space requirements. On the other hand, the industrial robot is a more capable piece of machinery in terms of payload and speed.
Higher Payload and Speed
For high-volume production and fast conveyors, a robot is better suited than a cobot, as it can operate at a higher pace. Another benefit of an industrial robot is that, once installed with fencing and safety measures, it does not require human supervision. Lastly, reach should also be considered an advantage for robots as they can palletize higher and need less programming to adjust for reach issues.
Costs in Cobots vs Robots
The cost of a robot or cobot varies significantly depending on the type of solution that works best for you.
Sometimes, a “turn-key” solution is what you will need, and sometimes customization is necessary. A turn-key solution for a cobot palletizer costs from €70,000, depending on the type of robot, gripper, software, and other components you choose. A turn-key robot palletizer can cost anywhere from €100,000 to €200,000, and this price may not include fencing and other installation requirements.
Palletizers
Palletizing is one of the many areas of application for robots and cobots, and in short, it involves placing products on a pallet for shipment or storage. It used to be, and still is for many small and medium-sized enterprises, a task performed by human labor.
It is a very repetitive and labor-intensive task that robots and cobots are gradually taking over, and this trend has led to a wide range of palletizers to choose from.
Six Common Solutions for Robot Palletizing.
- Palletizing Robots – a good choice for many, these are designed to carry heavy payloads and have a long reach. They are usually made with an axis coupling, which means that two or more of the robot’s joints are linked together. By doing this, it increases payload capacity and speed.
- 6-Axis Industrial Robots – These robots are more flexible and suited to perform a variety of tasks. They are available in various sizes, making it easy to find one that suits your project.
- Delta Robots – they are typically used as high-speed pick and place robots, but it is possible to program one to serve as a palletizing robot.
- SCARA Robots – Not all industrial robots are big. Scara robots are smaller robots with a payload capacity ranging from 3 to 20 kg. The Scara robots are designed to only move along the x and y axis, while the Z axis is locked in place. Usually used for light and detailed tasks, but can also be used for palletizing.
- Gantry Robots – Also known as Cartesian or linear robots, they are mounted on an overhead system that allows horizontal movement. They are capable of handling large payloads and typically perform pick-and-place tasks.
- Collaborative Robots – “Cobots” differ from traditional industrial robots in that they are designed to share workspace alongside people and are easy to operate. Due to this, cobots are generally smaller and slower. They are designed with smooth edges and come with an easy-to-use interface, which makes anyone a programming expert.
Cobot Palletizers
A cobot can go straight to work in the production area without significant changes to the production line and facilities. As stated above, the cobot palletizer must operate within certain parameters. For many enterprises, these are the deciding factors when choosing between a cobot and a robot:
- How fast is the conveyor?
- How heavy are the products?
- How high do you need to palletize?
These are all variables that need to be considered when going for a palletizing solution. For many small to medium-sized enterprises, a cobot is more than capable of handling all the issues above. Cobot palletizers are compared to robot palletizers as being easier to deploy, having a shorter installation time, and being easier to program. Flexibility is key.
Robot Palletizers
The robot palletizer has been around for decades and has proven its worth by efficiently processing large quantities and handling heavy products. This type of robot requires a fixed workcell and cannot operate alongside humans, as it performs operations at a higher speed and with greater weight. However, for larger organizations, a fully automated system with reduced human interaction may be beneficial.
The table below compares an industrial robot from Kuka and a collaborative robot from Universal Robots:
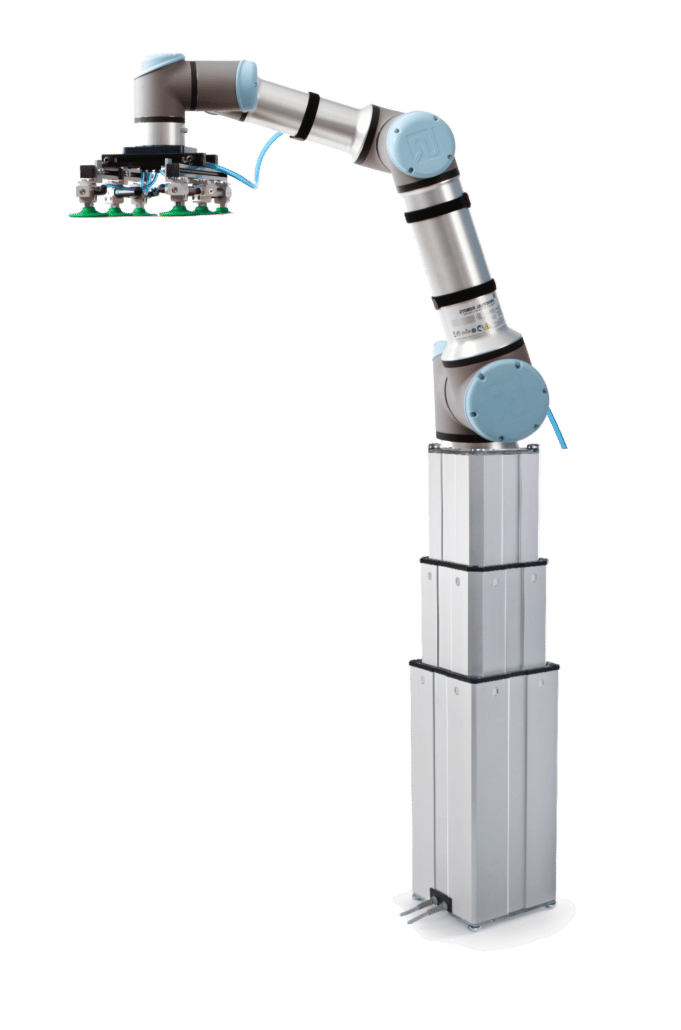
Factors | Industrial robot (Kuka) | Collaborative robot (Universal robots) |
Payload | From 40 to 1300kg | Up to 35 kg (UR30) |
Speed | Smaller industrial robots can reach 56 cycles per minute | Can reach 13 cycles per minute. |
size | Big. They need a lot more floor space due to fencing and safety measures | Require less space than an industrial robot. About the size of 2,5 pallets |
Re-use | Needs a heavy investment to move to a different task/location | Can easily be moved to another location |
Height | Up to 3,1 meters | Up to 2,4 meters without lifting column (UR20) |
Safety measures | Needs heavy fencing and sometimes extra sensors | Usually, without fencing. It may sometimes require additional sensors to control speed when humans are present |
Programming | Needs a specialist knowledge to program | Can easily be programmed with some training |
Installation time | Can be months | Can be done within two weeks |
Cobot vs Robot Palletizing
As shown in the table above, cobots and robots share many similarities. But at the same time, they’re not, because they’ve got their own individual strengths. These key factors should be considered when selecting a palletizer:
Price
As stated above, there may be a significant price difference between robots and cobots. An industrial robot requires a higher initial investment. It requires additional resources, such as floor space, and the organization must be financially capable of sustaining a more extended return on investment (ROI).
A cobot has a lower upfront investment than a robot, does not require the same amount of floor space, and has a shorter ROI due to lower costs.
In addition to upfront costs, there are maintenance and electrical expenses; the maintenance expenses vary significantly depending on the type of equipment used, and the electrical costs vary according to the size of the robot. Lastly, a cobot is significantly easier and less expensive to reprogram or modify for different tasks than an industrial robot.
Safety
The requirements for safety is a big part of the reason why industrial robots need more floor space, they need heavy fencing and sometimes extra sensors. A cobot is typically installed without fencing and extra sensors, allowing for installation with limited floor space.
Payload
The payload is one of the key strengths of an industrial robot. As stated above, the Kuka robot can lift up to 1300kg. When comparing this to the UR30 from Universal Robots, which has a maximum payload of 35 kg, the difference is significant.
Installation
This is where the cobot shines, as it can be installed in only one day. An industrial robot, on the other hand, has a significantly higher installation time, taking up to several months.
Read article: Short installation time and no downtime were a massive advantage for Aegir Brewery when they chose a cobot palletizer

What Should You Choose?
The facts suggest that there is still room for both industrial and collaborative robots in today’s industry. Even though it’s a tied race, you’ll see that the cobot is better suited for smaller product lines because of payload limitations, lower costs, and fewer requirements in terms of floor space and fencing.
Industrial robots are better suited to handle faster production lines and heavier payloads, but they also require more resources, including floor space and financial capabilities.
The lessons to be learned from this comparison are to understand that to choose between a cobot and a robot, you need to know and form an opinion about the key factors: installation, reach, payload, and price. Then you should be able to make the right decision for your business.
For further research on cobot vs robot palletizing, read this article.
Sign up for our newsletter and get a FREE ebook
By signing up for our monthly newsletter, you’ll get case stories, product launches, and tips to automate your production line!
Additionally, you will instantly receive an ebook about implementing palletizing. For more information, please visit our newsletter subscription page.
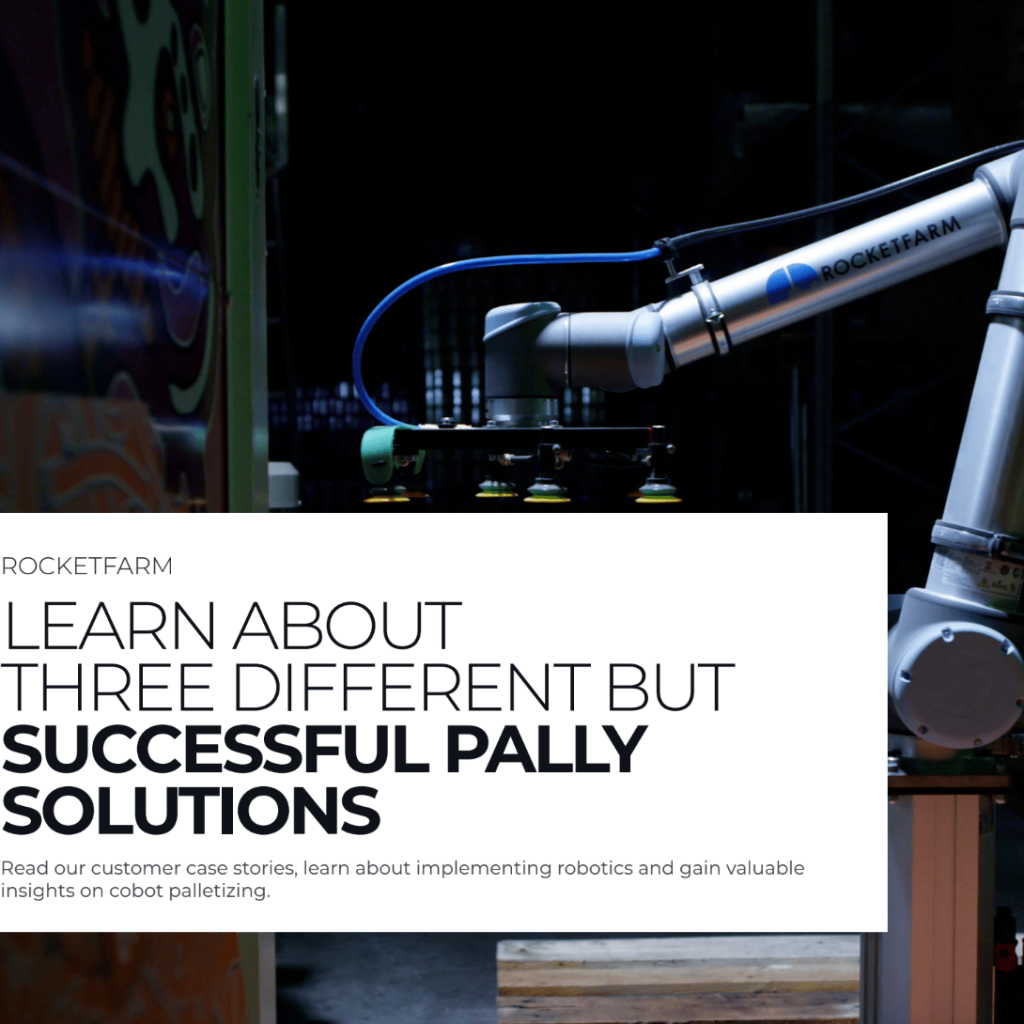