Want to install four palletizing solutions a day? Do remote installation like our Partner Kameleon in Norway. Recently they did their first all remote installation of a palletizing solution.
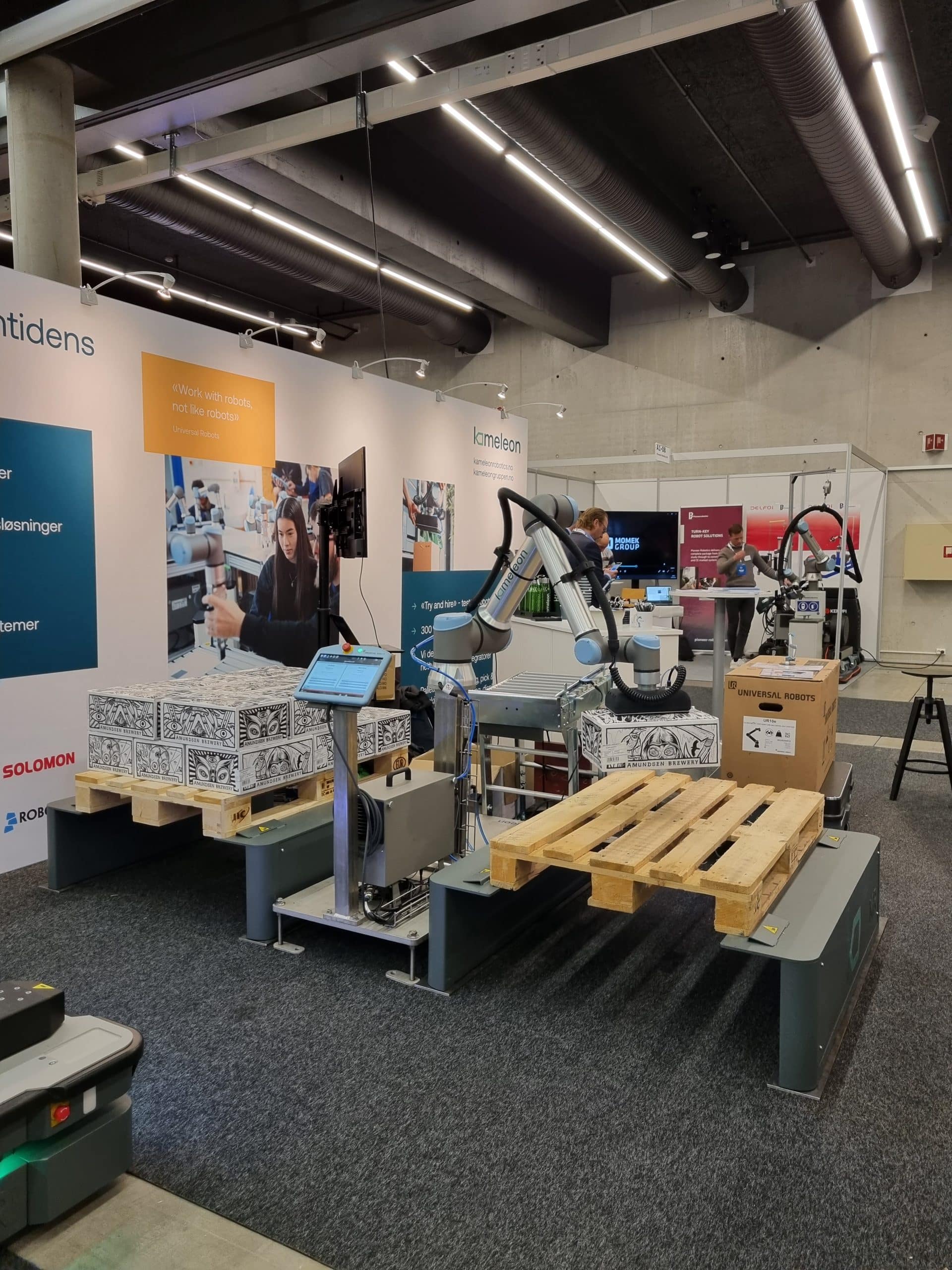
– During one working day, you suddenly have the capacity to do four installations per person. I think it’s quite tempting to do this again, says Emil Nissfolk.
Nissfolk is the technical manager at our Norwegian partner Kameleon, and tells us that the project started with them delivering all the hardware to their customer before the summer. At the time Kameleon wasn’t able to install the solution, because of missing pieces in the physical environment at the facilities. When the customer had gotten their palletizing space prepared for a palletizing solution, they got back to Kameleon and were ready for the installation. That’s when Kameleon got the idea.
Sees a great advantage
–the customer learns a lot more
Instead of travelling to the customer once more, they decided to use their experience from giving remote support to an installation.
– We do remote support on a daily basis. Practically all of our support is handled remotely with URsim and XMReality (Visual assistance software red.). So why not do an installation remotely as well.
Emil Nissfolk
CTO at Kameleon Robotics AS
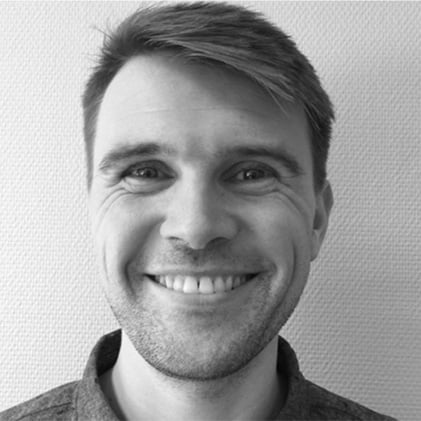
After some initial hiccups with permission-problems in the customer organisation when trying to use more advanced remote controlled software, they decided to return to their well known remote setup (see quote above).
“It’s basically us sitting with URsim on one side of the screen, and the customer walking around with a smartphone and filming everything they do on the other end. We’ll tell them what buttons to push, if their calibration is precise and everything they need to do. But they push the buttons. I see a great advantage in this, as the customer learns a lot more by doing it themselves,” says Nissfolk.
In this manner, Kameleon managed to get the installation up and running in just two hours of work. Yes, that was two hours of work to get a cobot palletizing solution to be operational. The speed of this is really incredible, and it opens up for whole new perspectives, where integrators can do up to four installations a day per person.
Out of the question without Pally
There are several reasons why a fast and remote installation like this is possible. We’ll walk you through three of the main reasons:
1: Kameleon has had a solution focus for several years.
They have packaged hardware that they trust and know together with Pally (Rocketfarms palletizing software red.) in a solution that they know what can do, how to install and how to support with the back of their hand. This allows them to shorten their sales and engineering work drastically, which means they can offer very competitive prices on a premium product.
2: The customer had a robot installed in their facilities from earlier.
Hence they were used to seeing a robot in the production line, and knew how the installation should look (they did all the physical installation). What they had never done before, was the installation. (Kameleon had done all of the installations and programming on the previous palletizing solution, so the customer had only done operational work on the robot).
3: Pally.
This current installation had two picking positions and several different patterns to be palletized. Without smart software to create the patterns and the code, it wouldn’t have been possible to do the remote installation. In fact it wouldn’t have been possible to offer the solution at the same competitive price, because it would have required extensive engineering to create the picking positions and patterns.
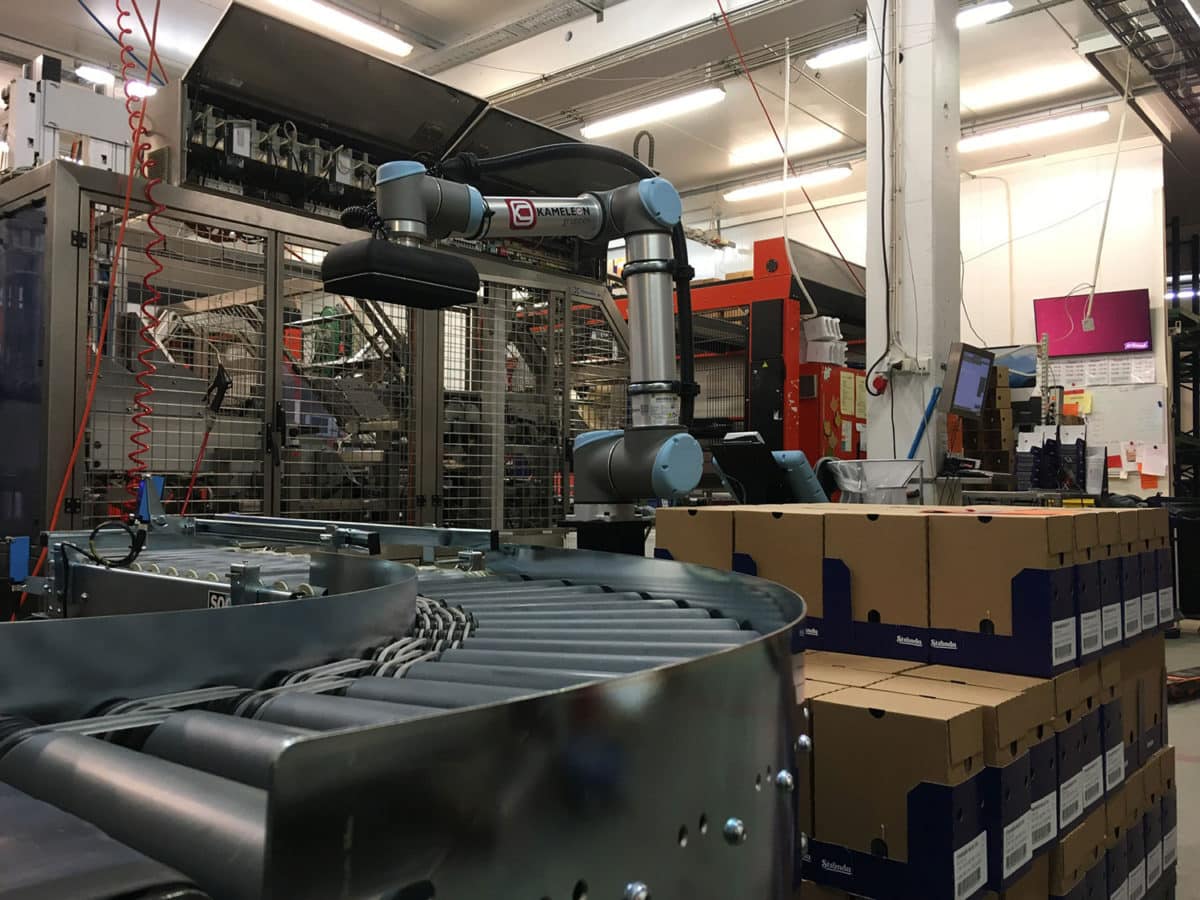
Not every installation is going to be done remote
Nissfolk is very honest that he doesn’t see every installation being done remotely any time soon. He enjoys the physical act of installing a solution at a customer, and not least the on-site training where he can get more and better feedback when he’s physically in the same room as the operators. But for specific cases, where it’s an advantage that you’re not physically there, the remote installation is a great option.
We see these as cases where remote installations are an advantage:
- When the customer already has a robot, is familiar with how robotics should be physically placed in their production line and the operators know what to do.
- Far away customers. If a customer is somewhere that requires extensive travelling to reach, remote installations could be a good solution for everyone involved. This equals saving integrator travel time, which also saves the customers money.
– The potential is endless
It might not be tomorrow or the day after. But remote installations are going to be a part of the future automation package. No doubt. Smart and application specific software is a huge advantage, as the user-friendly interface and simple instructions makes the remote installation much easier.
– We believe that Kameleon Robotics are embracing the future with their method. They have had a strong solution focus for many years and have improved their process to be able to offer a quicker, better and a more competitive solution to their customers. The potential with remote installations are endless. And it’s a path that the market should embrace, as it allows us to help more manufacturing businesses get automated.
Egil Mundal
CEO at Rocketfarm AS
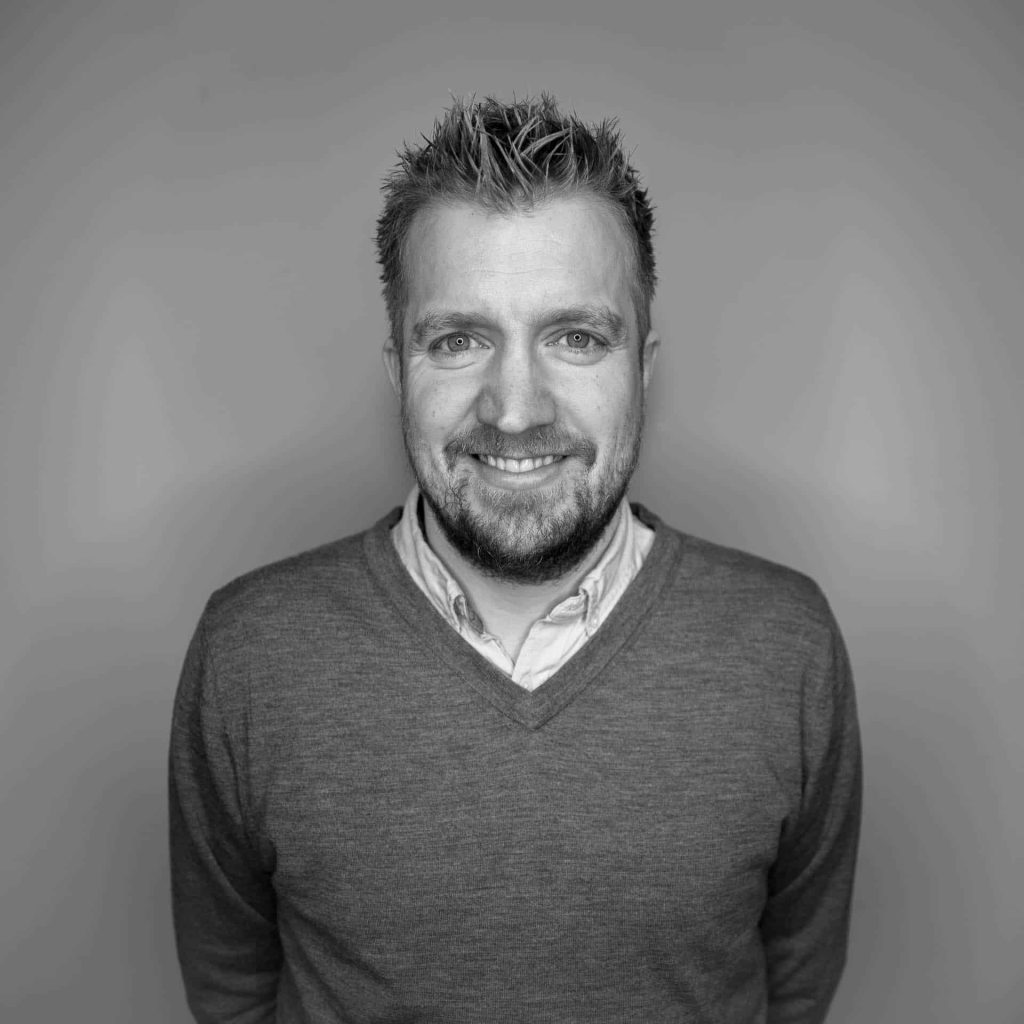
And we haven’t touched on the possibilities with digital twin technology. This case was only about how to digitalize the installation. Digital Twin Simulations offers many advantages pre- and post installation. The future is digital and software-centric.
Sign up for our newsletter and get a FREE ebook
By signing up for our monthly newsletter, you’ll get case stories, product launches, and tips to automate your production line!
Additionally, you will instantly receive an ebook about implementing palletizing. For more information, please visit our newsletter subscription page.
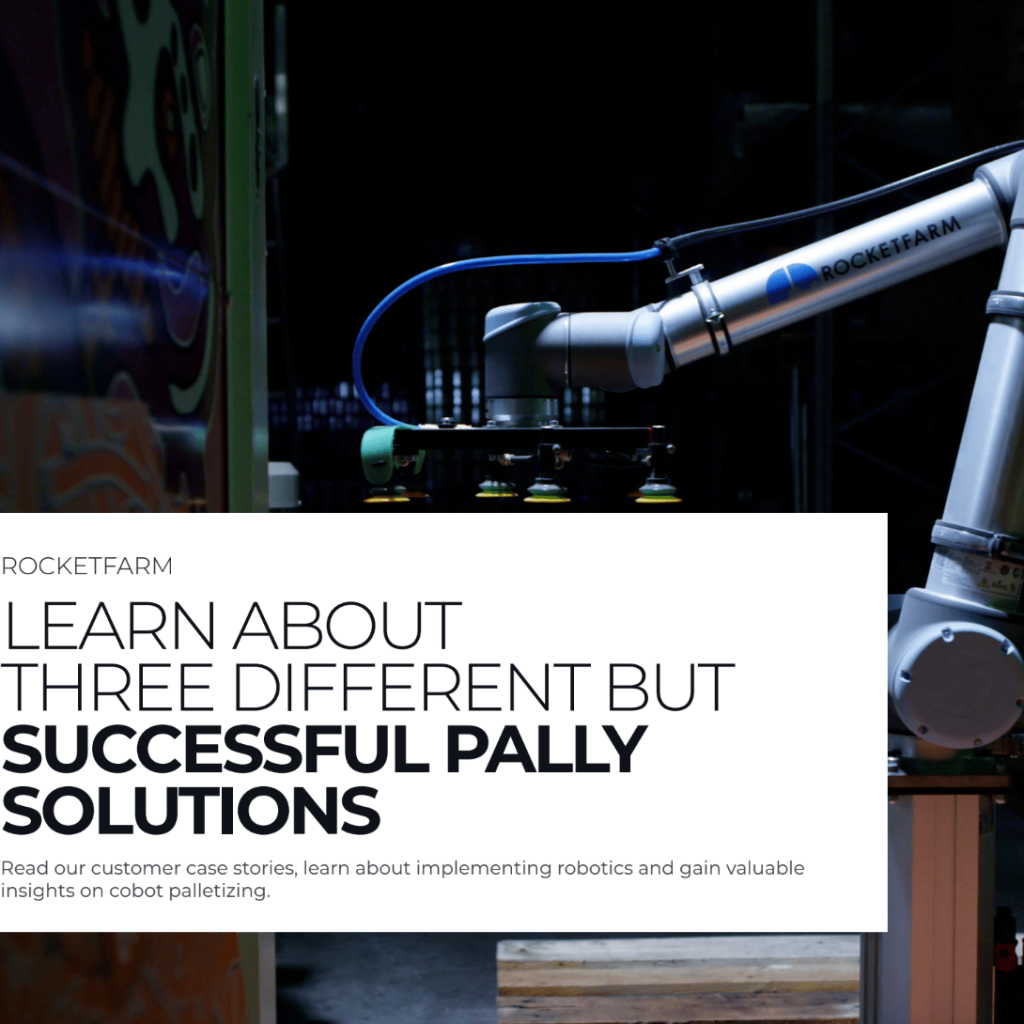