Hopefully, this article will answer some of your questions about collaborative robots and give sufficient insight into the technology. A technology that is sustainably changing human labor.
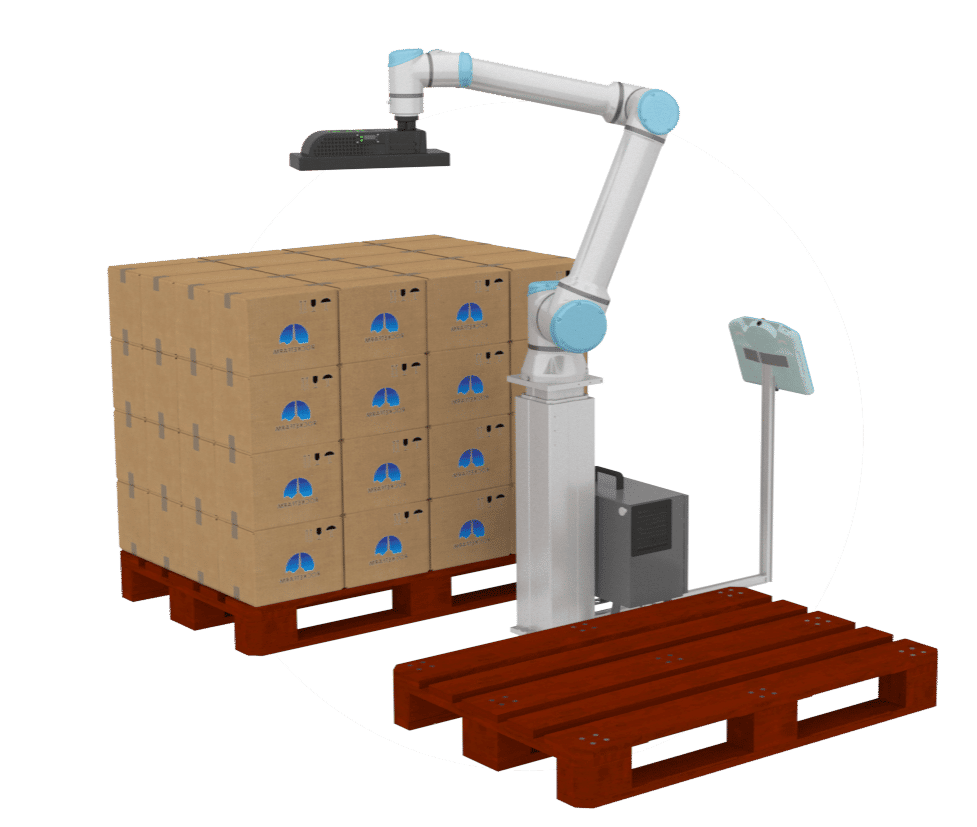
Collaborative robots, also known as cobots, are currently becoming a popular choice within automation. And there is a good reason for that.
Within the robotics industry, there have been major advancements affecting several sectors. This is forcing business leaders to pay extra attention to the possibilities with cobots.
This article will provide you with knowledge and insights about what a collaborative robot is. We are going to plunge straight into the technology that can optimize many different production tasks, look at the different pros and cons as well as the brands available.
We are also going to present real reasons why businesses choose to invest in cobots and showcase this by giving extra focus to one application field, palletizing, as this is our field of expertise and a great example of an application that can be automated with cobots.
So, what is a collaborative robot?
It is primarily about safety and flexibility. Collaborative robots differ from traditional industrial robots as they are meant to share workspace alongside people and are easy to operate. Because of this, cobots are smaller and slower. They are designed with smooth edges and come with an easy-to-use interface, which makes anyone a programming expert.
It is easy to learn how to program cobots fx. market-leading Universal Robots have a complete academy program you can follow.
Below, we’ll more thoroughly walk you through the different aspects of what you can expect from a collaborative robot
Payload and reach
Depending on the brand and type of cobot, there are differences between payload, reach, and motion capabilities. To give you an idea, the largest cobot from FUNAC can handle a payload of up to 35 kg and have a total reach of 1813 mm from base to wrist. In terms of motion capabilities, cobots have different sets of degrees of freedom. Between all different cobot brands, they can range from 4 independent aspects of motion all the way up to 14.
Detecting human presence
Cobots can be equipped with sensors that can detect nearby human presence. This feature enables it to reduce its operating speed or stop its production task to avoid a potentially dangerous situation. This allows employees to work inside the operating zone if needed, adding flexibility to the workflow without affecting the production line.
Adjustments on the fly
Additionally, with a well thought out software to accommodate the cobot, workers can easily make changes or adjustments regarding its production tasks while it is still operating. This is a huge advantage as it minimizes the downtime in production.
Low footprint
Another important feature is the cobots’ low footprint. Since cobots allow close possible interaction, it eliminates the need for large enclosures. This makes the setup fit in most production facilities, as the space required is small compared to other adjacent solutions.
The smallest Pally palletizing solution (UR Cobot) has a footprint as small as 0.16 sqm.
Very different from industrial robots
On the other hand, industrial robots, with which cobots are often compared with, are usually large, swift, and not suited for close collaboration with humans. These are designed for tasks that involve very high volume and require high operating speed. If you have ever seen a picture of car manufacturing assembly lines, there are usually large fenced robots that require expert knowledge for maintenance and programming.
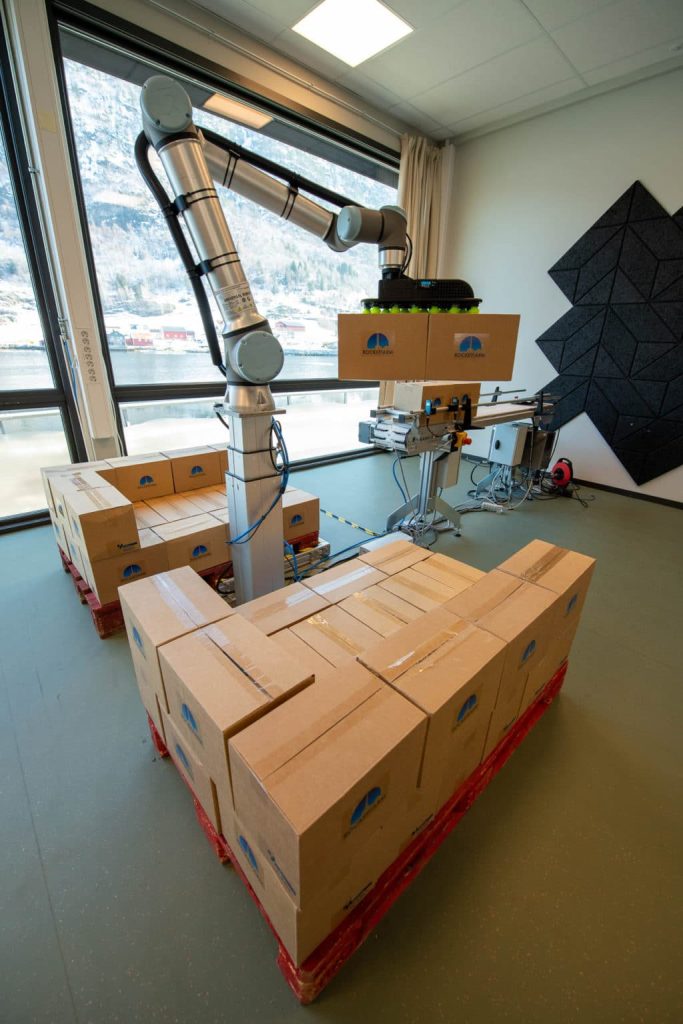
Pros and cons of cobots
Some of the advantages of using cobots have already been mentioned, but there is more. Cobots can, in theory, work all day, every day, increasing productivity and cost efficiency. Speaking of cost efficiency, cobots are cheaper than industrial solutions and can provide a return on investment within just 6 to 12 months.
They are quick and easy to deploy, both physical installation and programming. This also makes them flexible and able to change between applications if needed by changes in production. As cobots are cheaper and more flexible than industrial robots, they are highly relevant for SMEs.
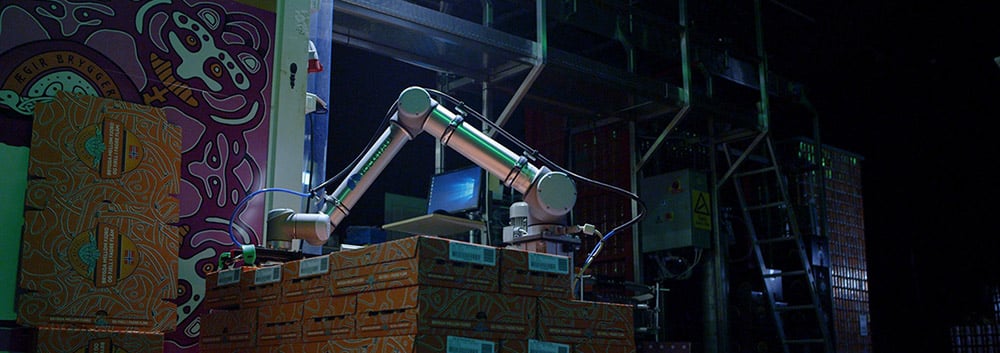
Customizable and precise
Since the cobots operate within millimeters, it ultimately increases quality. As it makes perfect repetitive movements, it will contribute to a high level of consistency in production. Furthermore, cobots are highly customizable, with many different hardware components to choose from, so you can pick the hardware components that suit your needs.
More satisfied employees with collaborative robots
For some businesses, integrating new solutions can feel like a difficult task and a nightmare to get used to. But this brings excitement and has been shown to contribute to a better working environment for employees in many different industries.
There are also ways to prepare your employees for automation to ease the transition.
If it wasn’t for our robot Stacky, I would have quit my job. I hate stacking cases of cases of cases on a f******g pallet.
Claus Bjerga
Packaging Manager, Ægir Brewery
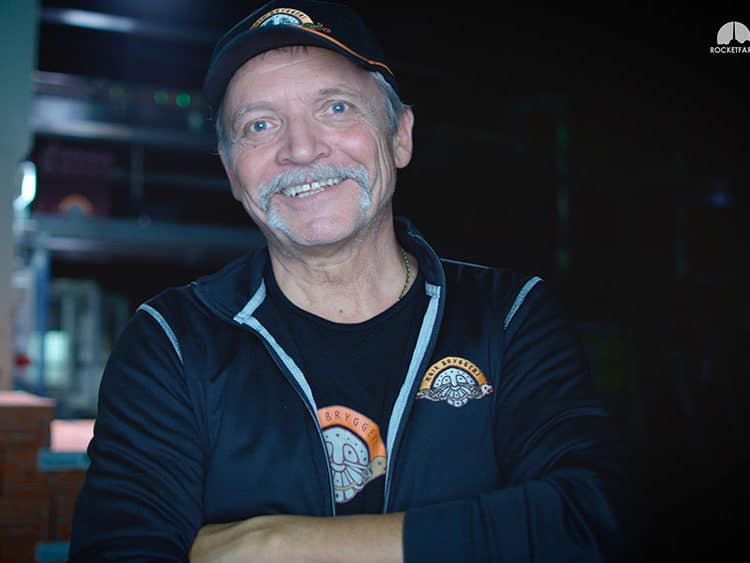
Cons of Collaborative Robots
On the other hand, there are some disadvantages to consider. The initial cost of the setup may vary, depending on the specific task. There are payload, speed, and reach restrictions on each cobot to ensure safety during human interaction. Because of its in-built safety features, it may reduce its operating speed or even stop its production task when it senses human interaction as too close and needs to be reset manually.
These limitations make cobots very well suited for smaller production lines (low volume/high mix) or very specific small tasks, while they are not very suited for high speed and high volume/low mix production lines.
What different brands of collaborative robots exist?
Similarly to industrial robots, there are many different companies and corporations that produce cobots. Some of the differences lie in the design, payload capacity, inbuilt technology functions and motion capabilities. Depending on the need for automation, businesses choose the ones that are best suited for the job. Examples of such cobot brands are ABB, Techman Robot, Yaskawa, FUNUC, and KUKA.
Universal Robots, or UR, is also a well-known and popular cobot brand. With over 50,000 cobots sold, UR is the leading manufacturer of collaborative robots, delivering high-quality performance and reliable products within several different industries.
These products include the UR3e, UR5e, UR10e, and UR16e, as well as the new UR20. Each has a different size and payload capacity ranging from 3, 5, 12,5, 16, and all the way up to 20 kg. In contrast to industrial robots, UR’s cobots are more compact and only weigh approximately between 11,2 and 64 kg. The UR10e is their best-selling cobot, as it covers a wide area of possible industrial applications
Why choose cobots?
Along with the advantages of investing in cobots, there are more reasons why choosing cobots could be a wise decision. By choosing Cobots, you are not only hiring a cool-looking colleague, but you are also setting yourself up to be more adaptive to future changes in production. As production will increase over time, you can potentially alleviate future bottlenecks within the production line.
Learn more about how we helped Nortura to future-proof its three cobot palletizing solutions here.
As a general rule of thumb, cobots are perfectly suited for handling low-volume, high-mix products. There are many situations where choosing cobots can be an advantage.
Examples of why businesses choose to integrate cobots into their production process can be if:
- There is a struggle to hire employees to do repetitive, unergonomic and/or heavy labor tasks.
- There is a limited budget, timeframe and/or or facility space.
- There is manual labor that requires humans nearby.
- There is a need for extra safety, flexibility, precision and/or consistency.
- There is a wish for an easy transition to automation.
Palletizing with collaborative robots
One example of how collaborative robots can be used is through palletizing. In simple terms, it is about getting the cobot stack cases on a pallet. But when you mathematically need to calculate coordinates for optimal pathways for each case to be stacked in a specific pattern and translate them into a language that the cobot understands, then it’s not necessarily as simple as you might think.
Our palletizing offering can help you
Before we launched our products to the market, we had learned (from an early palletizing installation in 2015) that the promised ease of use (in collaborative robots) was, in fact, not that great. This is why we built an algorithm that made this process easier by a mile and a half.
With our PALLY software and the next-level industrial automation platform – MyRobot.cloud, you have the ability to program new products to be palletized within minutes easily.
This solution is the leading palletizing software for UR cobots in the market, making palletizing available for anyone without prior knowledge of robotics.
Employees don’t like to palletize
If you don’t like stacking cases like the production manager at Ægir Brewery, then palletizing with cobots has been shown to ease the frustration. Not only that but also optimizing the palletizing process significantly at a lower cost compared to traditional palletizing solutions.
Using cobots for palletizing helps employees avoid serious injuries in the future. While reducing repetitive, strenuous, and tedium work, they ultimately have more time to work on other, more important tasks.
As you might have read earlier in the article, Claus, the packaging manager at Ægir, would have quit his job if it wasn’t for their collaborative robot palletizer.
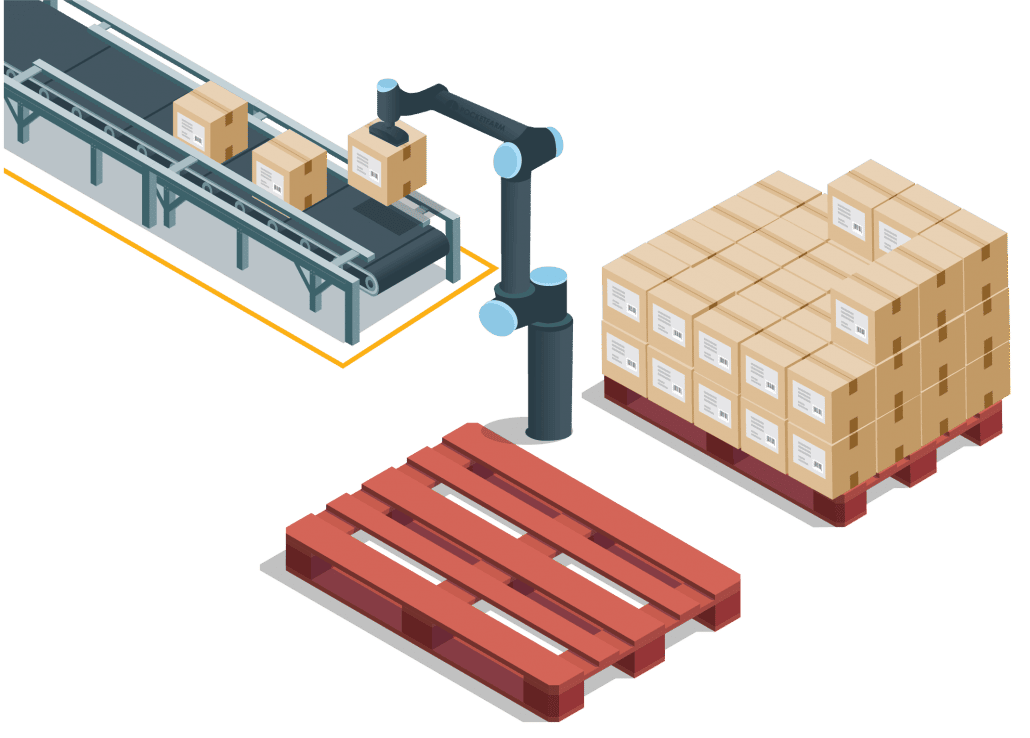
Many benefits to collaborative robots
To summarize, we have talked about many different reasons why choosing cobots can be beneficial. This ranges from cost-efficiency, flexibility, and safety to its ease of use and deployment. We also know that there are some restrictions to cobots that are worth noting, like its payload, reach, speed, and motion capabilities. Finally, we provided an example of how palletizing is a perfectly suited task for cobots.
Interested in adding a cobot palletizing solution to your production line? Learn more about Pally Palletizing Solutions here
Untapped potential
As we can imagine, there are many untapped possibilities when it comes to cobots and their future. Throughout this article, we hope that you have gained a better understanding of the technology that has the potential to shape the future of production.
Sign up for our newsletter and get a FREE ebook
By signing up for our monthly newsletter, you’ll get case stories, product launches, and tips to automate your production line!
Additionally, you will instantly receive an ebook about implementing palletizing. For more information, please visit our newsletter subscription page.
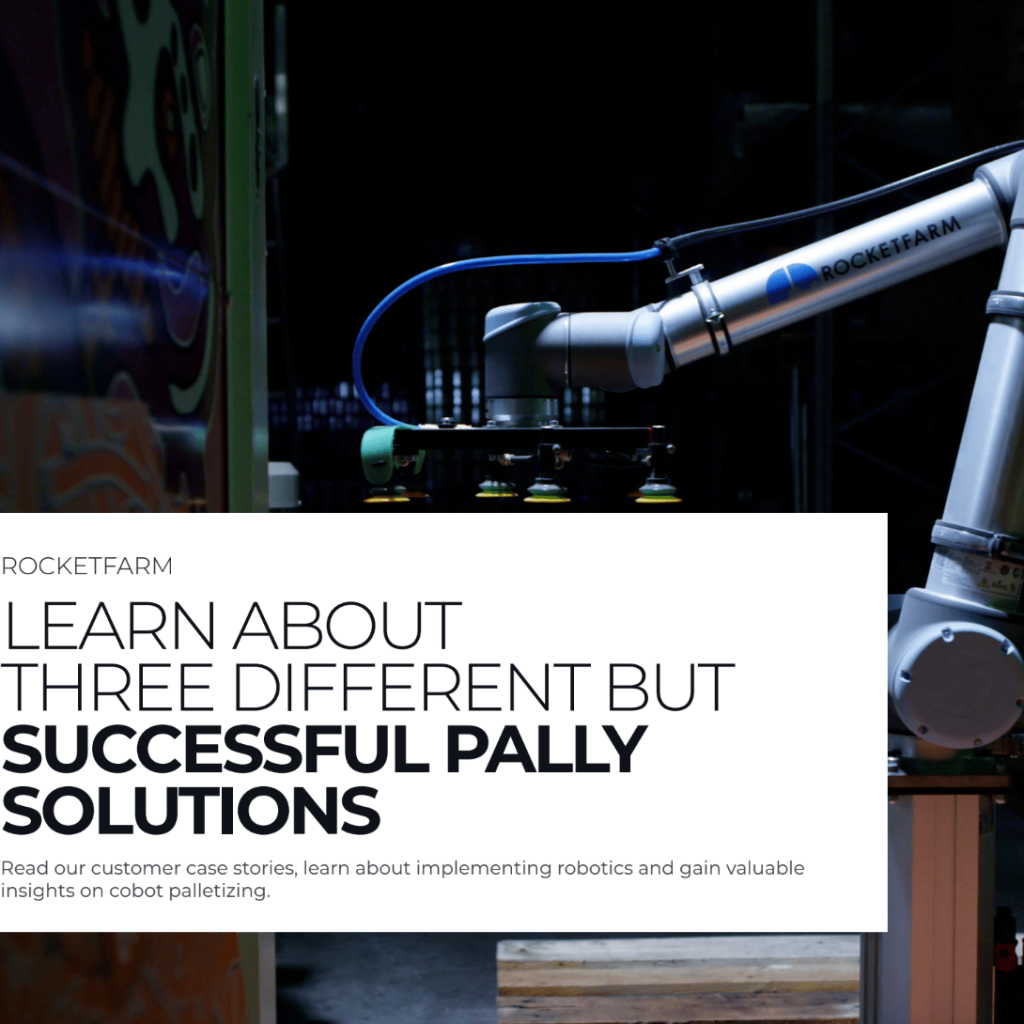