This article will look at the principles of palletizing, and more specifically – the cobot palletizing principles. We will discuss what principles you need to be aware of in order to understand and choose the best cobot palletizing solution for your product.
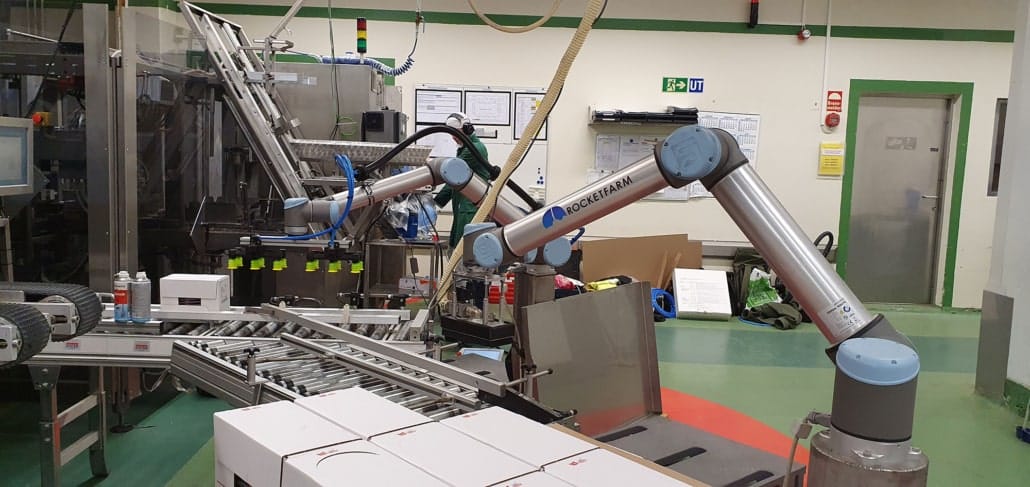
Stacking pallets of cases for direct distribution or storage has been around since the first packaging lines were installed many moons ago. And the process of palletizing is still a manual task – in most manufacturing companies.
Today, due to labor shortage and a larger emphasis on the work environment, there is a movement toward cobot palletizing.
It is a fact that each palletizing process is different. Therefore, the best cobot configuration is unique for each project. Luckily, there are many different options to choose from. Because of this, manufacturers can have a cobot solution that is optimal for their palletizing process.
If you want to know more about the differences between a cobot- and a robot palletizer, check out our blog post on robot vs cobot palletizers.
Palletizing Equals Heavy Lifting
Let’s discuss the reasons for automating palletizing tasks, before we move on to the cobot palletizing principles.
The process of palletizing contains repetitive motions and can often include heavy lifts. There is an increasing demand for a healthier and more efficient palletizing process, due to the ever-increasing need to palletize.
Having an employer do these tasks is an unnecessary risk for both your employee’s health and wellbeing at the workplace. The value of an employee is not exploited when they are required to do repetitive and strenuous tasks like palletizing.
Human employees can do these tasks, but at the same time they can create much more value if they are allowed to use their knowledge and skills on more interesting and challenging tasks. The motivation of employees can be increased, by giving them tasks that are challenging and interesting.
Increase your employees motivation
Automating the palletizing process can however have more effects than simply increasing productivity.
Having motivated employees brings several benefits. Beyond the Clock: The Benefits of Highly Motivated Employees points out some of these benefits – including higher productivity and performance, a greater level of creativity and innovation, increased employee engagement, and other factors that often can make a company successful.
Automating the palletizing process can, in fact, increase employee motivation. As pointed out in this article, motivated employees can have a great deal of positive effects. Communication with employees, can help a manufacturer predict how automating a palletizing process will be perceived by the employees.
If you have questions regarding effects of automating the palletizing process, or any other questions, please contact us!
We will be happy to talk with you.
Configure your specific cobot setup
We have now expressed some arguments regarding why you should automate the palletizing process. Read on to learn more about cobot palletizing principles, and factors to consider when selecting among different configurations.
The process of purchasing a cobot palletizing solution can in fact be quite similar to the process of buying a kitchen.
The need of a new kitchen occur when the old one is outdated, or your needs might have changed because of other upgrades in your home. Sometimes it is enough to upgrade parts of the kitchen. Other times it is necessary to replace the whole thing. When browsing for upgrades, you have many different options. It is possible to buy complete solutions, but often you are able to personalize and create your perfect kitchen.
With the purchasing process for buying a kitchen in mind, we can take a look at the process of buying a cobot palletizing solution.
When looking at automating a palletizing process, there is a great range of different configurations. Due to the differences among palletizing processes, some require vacuum grippers, while other needs pneumatic grippers. Some product lines have limitations of footprints, while others want a big solution that perhaps can have a higher payload.
Most Essentail Principles
Below is a walk-through of the most essential cobot palletizing principles. Consider these principles being some of the essential parts in your kitchen. You can choose among several different components, in order to get the solution that fits your exact needs.
1: Payload
The payload is the weight of the item(s) in which the cobot have capacity to palletize.
In palletizing, the payload capacity is essential. The weight of the item that is needed to be palletized, can not exceed the payload capacity of the cobot. These are widely known cobot palletizing principles.
If factors like payload and gripper (learn more about grippers further down in the article) allows it, a cobot can pick and palletize multiple cases at the same time (as in the example to the right). Multipick has a big impact on the productivity and safety of the palletizing solution, but it always has to be within the total payload capacity of the cobot.
When calculating the payload, the weight of the gripper needs to be subtracted from the cobots payload capacity. The weight of a gripper differs, and ranges from less than 1 kg, as this one from Joulin does – to over 2,5 kg. Normally a vacuum gripper range between 1,5 kg to 2,5 kg.
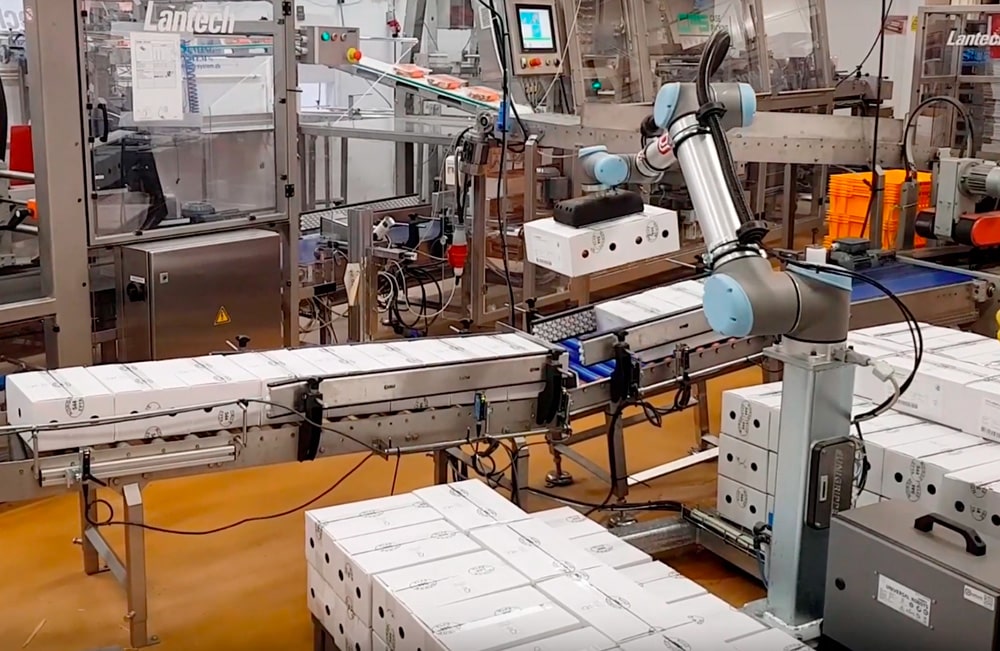
2: Gripper
The gripper is an essential part of a cobot palletizing solution.
There are numerous different grippers to choose from, with numerous different features. It is important to choose wisely, so you’ll get a gripper that suits your needs. You can choose between vacuum grippers, servo-electric grippers, pneumatic grippers and hydraulic grippers.
In the following section, we will introduce two types of grippers that are often used for palletizing.
Recommended grippers
For palletizing, we at Rocketfarm recommend choosing a vacuum gripper. We recommend a vacuum gripper because it allows you to take full advantage of Pally and its Smart Grip benefit. Some great vacuum grippers we recommend for palletizing are: Schmalz FXCB and Piab CPT.
“Vacuum grippers with foam are excellent for palletizing tasks where the dimensions of the products may vary”, Bjørnar Dale, Automation specialist at Rocketfarm
3: The Footprint
Since space is usually a valuable resource in production facilities, the footprint of a cobot palletizing solution is of great importance. It is often seen as one of major advantages with a cobot. It is the pallet(s) rather than the cobot palletizing solution, that takes up most of the space.
Most of the cobot palletizing solutions do have a dual-pallet setup, which allows the cobot to immediately start palletizing when the first one is done.
A Pally Palletizing Solution can have a footprint as little as 0,16 m2 + pallets.
A cobot also has the ability to be connected with safety sensors, which detect if an operator steps in the area of the palletizing cell.
The sensors can detect the operator, and let the cobot know to slow the speed down, while they are inside the workspace. Therefore, it is not necessary to use fencing that requires extra space. This also allows your employees to work safely – close to the cobots.
Naturally, these possibilities brings some limitations.
Since a conventional industrial robot can operate at a faster pace, it is better suited to high volume production and fast conveyors than a cobot. Cobots also needs some human supervision. However, cobots have smaller footprint, short and easy installation time, is more agile and often a cheaper alternative.
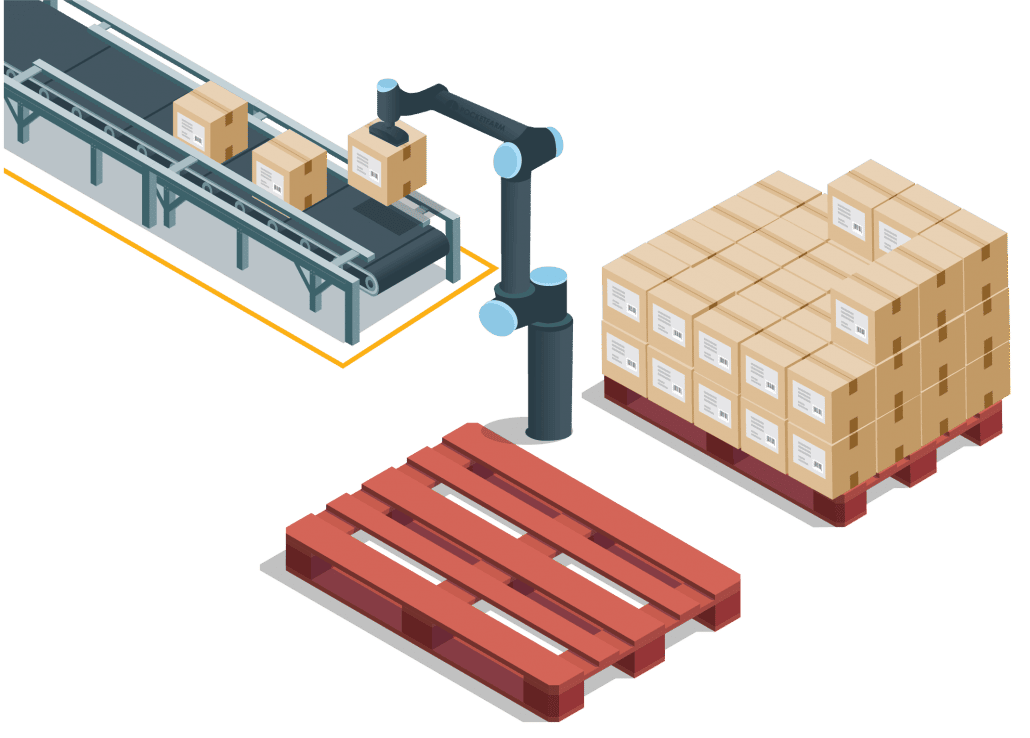
4: Digital twin simulations for cobot palletizing
Many people want to visualize the solution before investing in a kitchen. We see the same need for cobot buyers.
MyRobot.cloud—Fast Track to Cobot Palletizing offers Digital Twin Simulations of solutions based on basic information about your production. It is a free-to-use platform that will validate the feasibility of cobot palletizing solutions that fit your automation needs.
This way, you’ll get visualization and confirmation before buying. It will also suggest a solution provider for you based on your region.
Instead of spending time and money on expensive consulting hours, you can swiftly and painlessly get a verification.
A shareable link to a complete project analysis in an easy-to-understand report will be sent to your inbox within one hour.
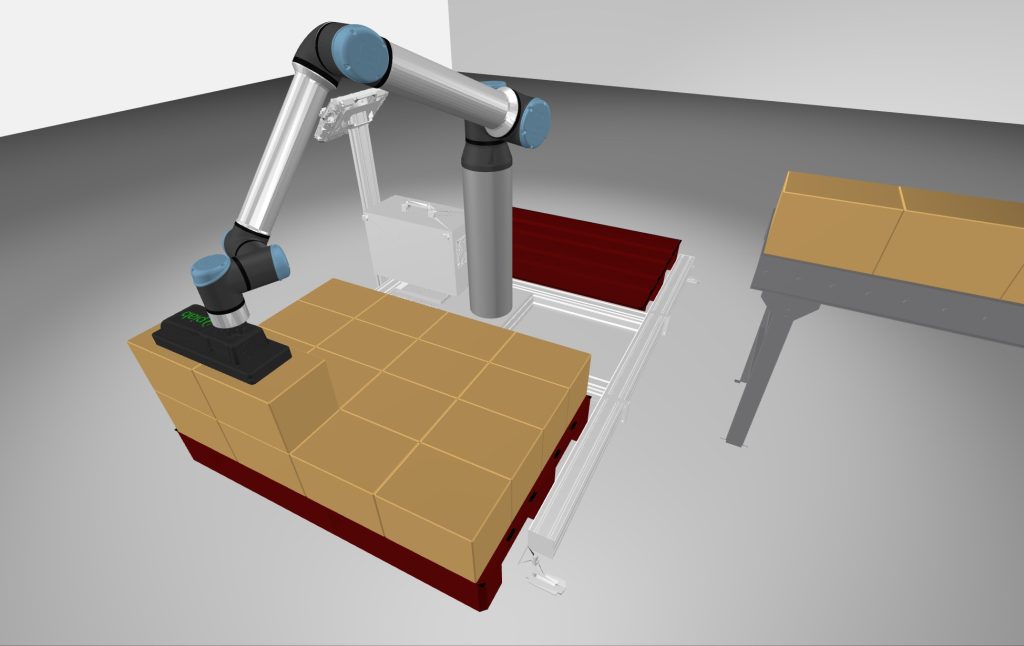
6: Safety
We are coming to an end of this article, but before we wrap things up, we need to talk about safety.
Safety should indeed be a prioritized factor for manufacturers. Cobots are designed to be safe around people, and that is what makes them collaborative.
However, they are only safe as long as you use them in a safe manner. This may sound subtle, but the reason that they are safe, is because they are designed to comply with safety standards. This involves adjusting the cobot accordingly to your palletizing application. Therefore it is necessary to do a risk assessment of a palletizing application.
In collaborative robotic systems, ISO/TS 15066 provides guidelines and is presented by Association for Advancing Automation. The guidelines are a technical report written by ISO and is expected to become a standard.
They offer great help towards making a risk assessment for a cobot palletizing solution (and other cobot solutions).
Important: We recommend using the expertise of Pally Approved Partners to help with safety and risk assessment. They have the knowledge and experience needed, to create a safe and thought through risk assessment.
Pally Palletizing Solutions has the most advanced multi-pick functionality in the market.
-This allows you to lower the speed of the cobot, while still reaching your desired CPM. As speed is the most important factor in the safety assessment, this will make a Pally Palletizing Solution a safer choice for your production line.
In conclusion
There are several factors to consider when looking at cobot palletizing principles. Before automating your palletizing solution, it is natural to look at why you should invest in it – or not.
In this article, we have pointed out increasing productivity and supporting employees as examples of arguments to do so.
Each palletizing project is different, and it is therefore common to need a different cobot configuration for different projects. Due to different needs, it is possible to configure a big range of palletizing solution.
Some needs high payload, other value speed. It is possible to select among different grippers, footprint and payload.
With software from Rocketfarm you are able to optimize pallet patterns, which can have positive effect both on productivity and safety. With the Fast Track to Cobot Palletizing, you are also able to get an upfront verification of a cobot palletizing solution for free. This way you know what you get before buying.
Sign up to our newsletter and get a FREE ebook
By signing up to our monthly newsletter, you’ll get case stories, product launches and tips to automate your production line!
Additionally, you will instantly receive an ebook about implementing palletizing. For more information, please visit our newsletter subscription page.
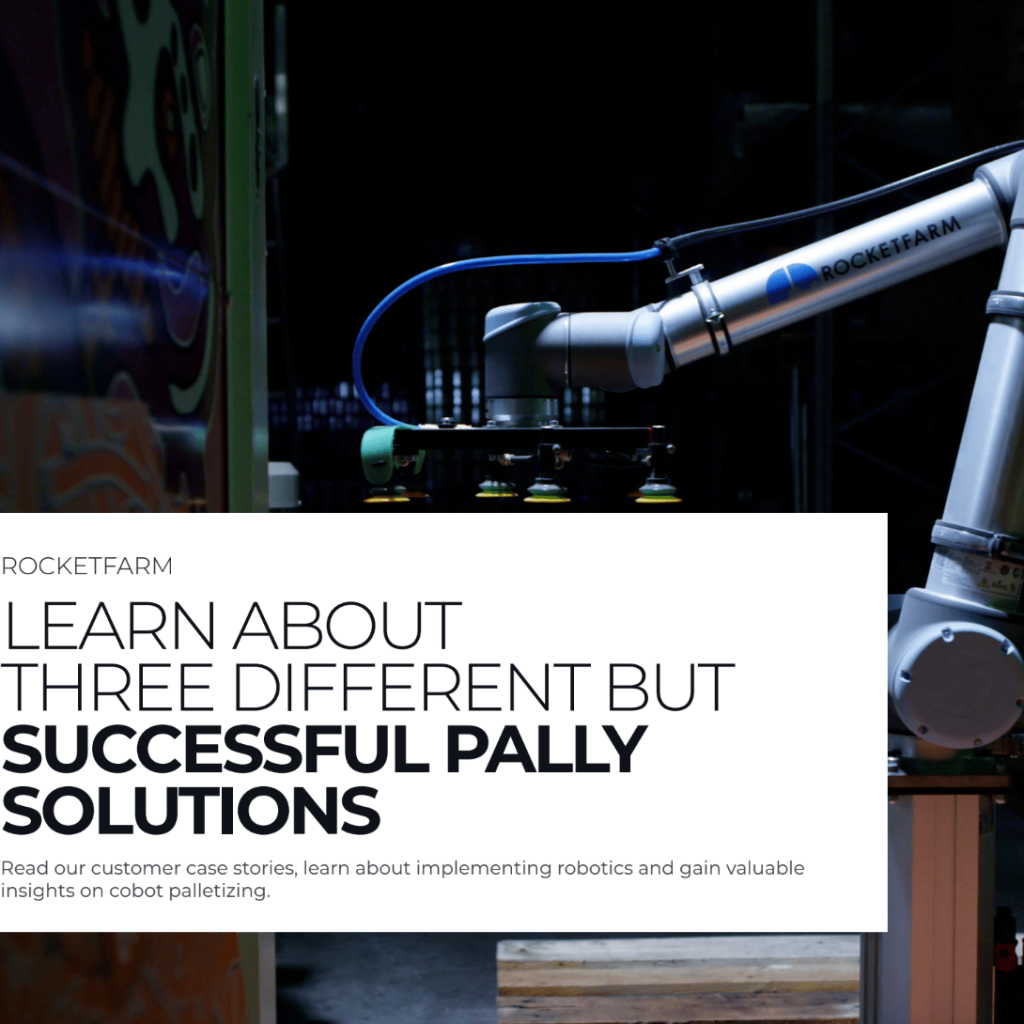