In this article we have gathered four of our best tips to help you solve reach issues in cobot palletizing.
Because there are many advanced components that needs to work in tandem to make the solution function properly – and the most common issues you can encounter is connected to its reach.

Why does reach issues appear in cobot palletizing?
Before we start listing tips, it’s beneficial for you to have a basic understanding of why reach issues appear at all. So let’s begin with that before we get into more technical details.
Every palletizing project is unique.
Ideally, a palletizing software should be able to determine the best way to place the boxes onto pallets. But this is not always the case. Some of them needs more advanced configurations, rather than using default setups to ensure optimal reach.
One obvious reason for why some projects encounter reach issues, has to do with the cobots total length. But this is actually just one of several factors that affects the reach.
In simple terms, it comes down to these factors:
- The type of cobot
- Its mounting
- The gripper
- Weight and size of the boxes
- The way the cobot choose to place the boxes onto the pallet
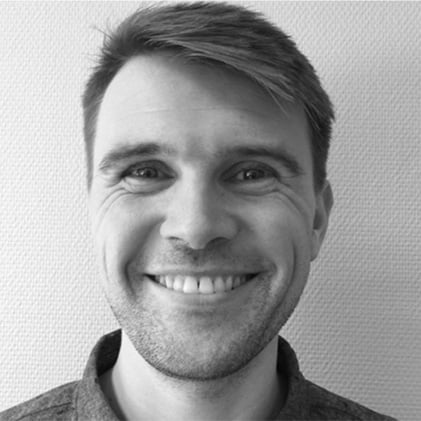
Common solutions to solve reach issues in cobot palletizing
Some of the tips we are about to present, are specifically drawn from Pally, our palletizing software. If you are using Pally, you can easily make new software configurations to increase reach by using our developed features.
The tips will also work without Pally. But it is important to note that you will need a bit more knowledge, time and effort, unless the software provides you with similar flexibility for palletizing.

With Pally, you can easily adjust to new patterns without the need for engineers. This saves you from unnecessary downtime and new costly installations.
Brigt Grepstad Røysum
Channel Executive at Rocketfarm AS
With these tips, you’ll be guided through certain actions that you can try for yourself. Hopefully, these will prove helpful in solving your specific reach issue.
1. Investigate software configurations for the gripper
First and foremost, we recommend start searching for possible solutions with the setup you already got. If you can solve the issue through software, you’ll save yourself from any additional costs.
We’ll start by looking at the gripper and how it pick up boxes, which affects the placement.

Here are some actions you can try regarding the software configurations for the gripper:
The gripper orientation is a feature that allows you to choose the exact direction of the gripper when it picks up boxes (front, back, left and right). By changing the gripper orientation, you can potentially increase the reach of the cobot, when placing the boxes.
This is especially true if you are using a gripper that can provide you with some extra reach (typically oblong or big grippers).
Note: As an alternative (if possible), you can also change the direction of the box on the conveyor.
The gripper optimization is a feature similar to gripper orientation. Only this allows the software to calculate the best directions for the gripper to pick up boxes.
Within the Pally software, you can choose between None ( Same as “front”), 2_way (same as “front” or “back”) and 4_way (all directions possible). Enabling one of these can potentially solve the reach issue.
2. Investigate the pattern and its layers
This second tip can also potentially save you from any additional costs. By looking into the box pattern of your pallet, you can make small changes that can solve the reach issue.
Move boxes closer to each other. If you have a pattern with unnecessary spacing between boxes, closing the gaps can help with the reach issue. It also enables you to multi pick boxes, which can also increase the reach of your cobot.
Switch first and second layer. If you got an interlocking pattern where every other layer is mirrored, you can try to switch them to see if this will solve the issue. Considering the location of the edge boxes on the different layers, there could be a layer that is more suitable to be placed first.
Rotate or mirror the whole pattern. This is worth trying if the pattern is asymmetrical, to get the boxes closer to the cobot.
Inverted approach is a feature that allows you to change the order of which boxes to be placed first. This will determine in which direction the cobot is building a layer, as well as the directional approach for final placement.
Having inverted approach disabled (default), the cobot will use a logical approach, starting a layer by placing a box in the furthest away corner of the pallet. This will in some instances solve reach issues, especially in the top layers, as it doesn’t need to lift boxes above previous placed boxes.
By enabling the inverted approach function, you’ll allow the cobot to use an illogical approach. This way it will be able to lift boxes above previous placed boxes. A layer can then be build starting from the corner closest to the cobot, which sometimes can be beneficial. This approach may cost extra time and result in less reach, but in return it can create extra space to move smaller boxes closer to the cobot.
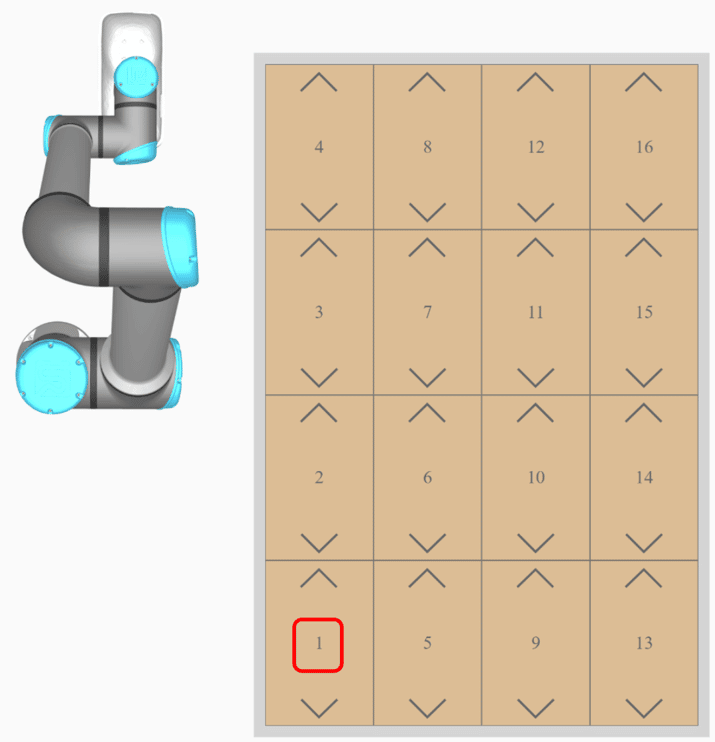
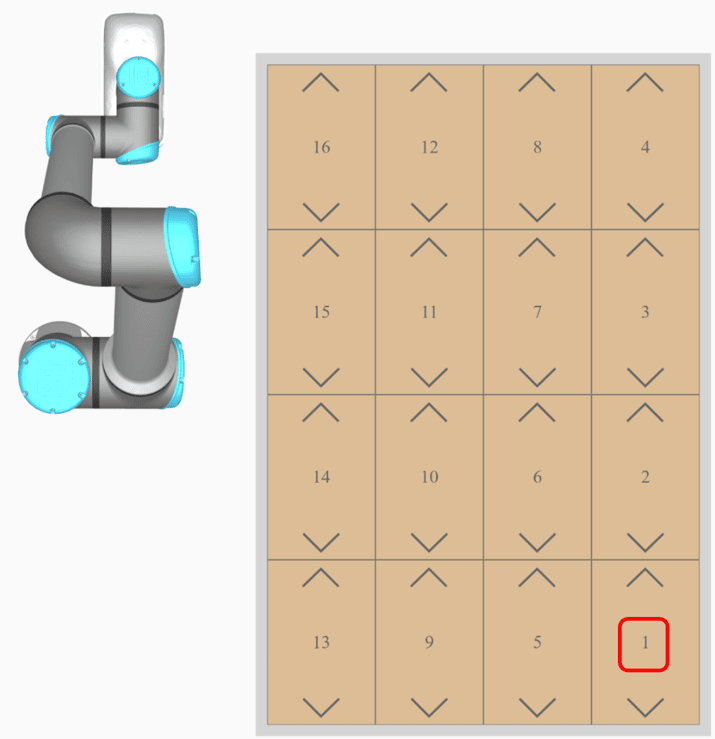
Generally, enabling inverted approach will give the cobot less reach but have better maneuverability to place boxes closer to the cobot. Having it disabled will maximize its reach but at the cost of maneuverability.
This shows the complexity involved in palletizing, and the easiest way to test and evaluate, can be done through simulations.
3. Talk to experts
At this point, we would advice you to get in touch with a palletizing expert.
Even though you are becoming more of an expert reading this article, it would be wise to consult someone for a second pair of eyes to look at your situation.

If you run the Pally software on your UR cobot, you can also use our web-based robot programming tool, MyRobot.cloud. This means that you have access to a powerful tool that gives you the freedom to make complex changes in the palletizing program in an easy way.

Create, add, and upload new patterns in a few minutes without production downtime. With just basic information about your product specification, you can design the pallet pattern of your choice and program new instructions to your cobot. Alternatively, you can import your current UR palletizing field and start working from the current UR palletizing file.
If you encounter reach issues, you can easily try the suggested solutions presented above.
4. Investigate hardware configurations
With this final tip, we are now moving over to getting extra hardware to be able to palletize you specific project. If none of the two first tips helped you, getting new hardware may be the only solution.
Adding an offset bracket could be a quick fix to further increase the reach of the gripper.
However, this would also affect the payload limit. So make sure the weight is still supported by using an offset bracket.
To give you an idea, the graph illustrates the relationship between accepted payload and the center of gravity offset for a UR10e cobot. This has to do with the warranty of the cobot.


Installing a lifting column can in many cases solve reach issues, as it provides an extra axis for the cobot to move.
We often recommend investing in a lifting column, as this provides you with a lot more flexibility for palletizing future projects.
Choosing a different gripper can be a great option, as not all grippers are the same. They vary in shape and size, and some of them are better suited for palletizing than others.
Similarly to the lifting column, this will also give you some extra flexibility to palletize and adapt to future projects.
Learn more about Universal Robots palletizing configurations
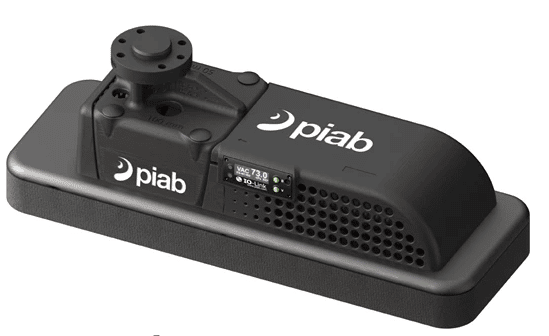
Conclusion
We aim to make the palletizing software as easy to use as possible.
In most cases, the software will calculate the best options for you. But sometimes, it is difficult with all kinds of possible palletizing projects.
With Pally, you can make quick changes in the program using MyRobot.cloud to solve issues and avoid extra costs by buying new hardware. In other words – there is a lot that can be done to try to solve reach issues in cobot palletizing by investigating what you already have.
Looking into software should, therefore, be your first priority. But if your current setup proves insufficient, looking into new hardware may be the only solution.
Sign up for our newsletter and get a FREE ebook
By signing up for our monthly newsletter, you’ll get case stories, product launches, and tips to automate your production line!
Additionally, you will instantly receive an ebook about implementing palletizing. For more information, please visit our newsletter subscription page.
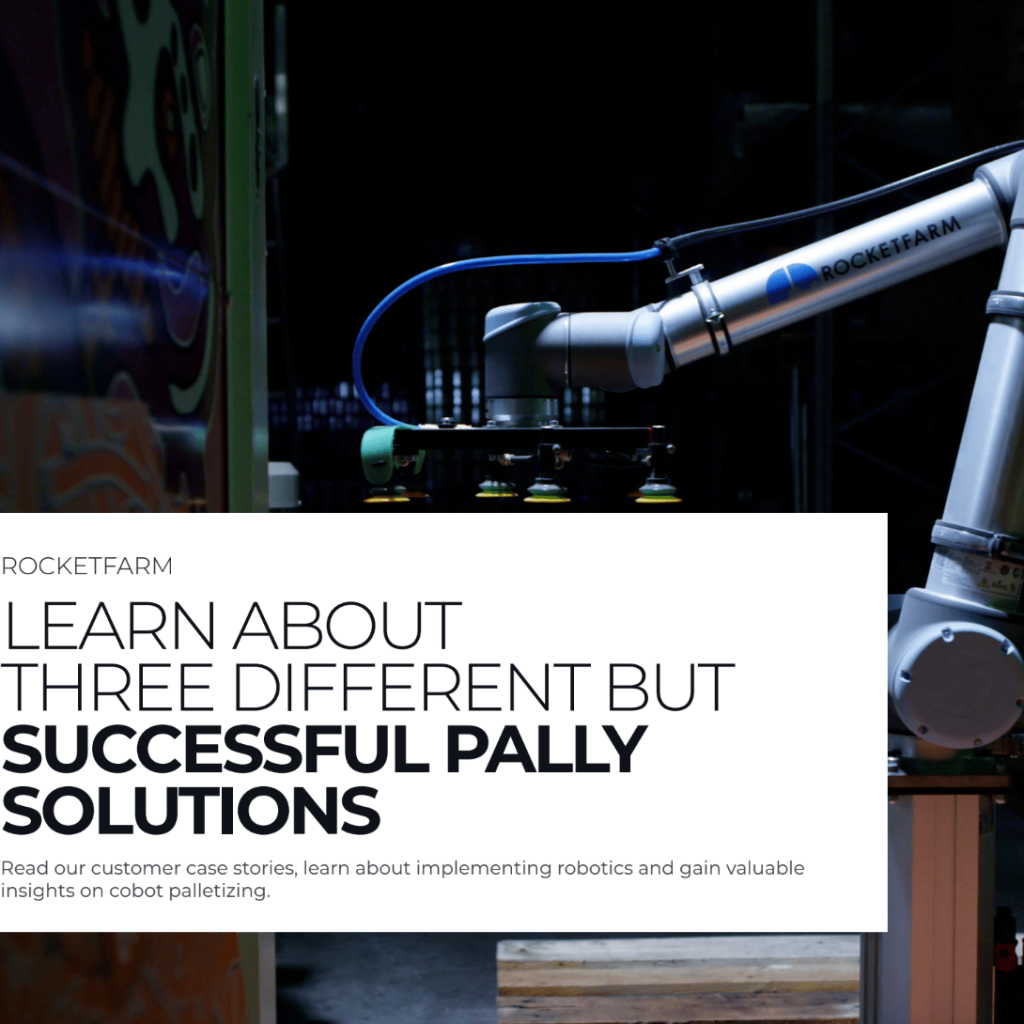