This article will focus on what you actually pay for in a cobot palletizing solution. Whether you’re new to cobots or looking to upgrade your current system, this article provides insights into to what you should know before buying.
Because what you pay for is more than just a robot.
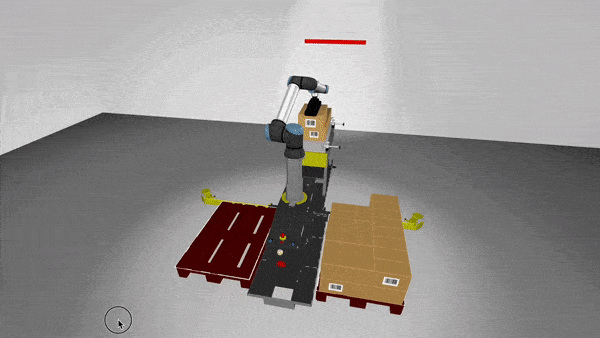
Even though there are many automation applications, packaging and palletizing solutions remain among the most likely use cases.
To meet this growing demand, many companies are turning to collaborative robots, or “cobots, “ to improve the efficiency and productivity of their facilities. With their ease of use, flexibility, and low cost, cobots have become popular for small and medium-sized businesses looking to automate their production lines.
Recent years have shown a growing number of manufacturing companies looking for automation. According to the results from the 2022 McKinsey Global Industrial Robotics Survey, automation will account for 25 percent of industrial companies’ capital spending over the next five years.
Robot
Starting with the essentials, the first thing to consider is the type of robot you need. Using the Universal Robots as an example, their cobots are great for palletizing.
The UR10e has been on the market for some time and has proven its effectiveness in palletizing. The other alternative is their latest UR20. This cobot is their most robust robot, with a max payload of 20 kg and increased reach, making it perfect for palletizing.
The different sizes of cobots naturally have different costs, but the price of a cobot is significantly lower than an industrial robot. With either of these cobots, you can be sure you will get a high-end product that enables various applications.

In addition to the footprint, reach, and payload differences, there are other differences like torque, operating speeds, and weight.
In many ways, you don’t just get a robot. You get an employee that can provide your organization with numerous benefits. This can range from improvement in the work environment to increased cost-effectiveness and safety.
The cobot palletizing solutions are the robots we have with the highest operating time and lowest running costs.
Inghild Lysne Sanden
Factory Manager Nortura Sogndal
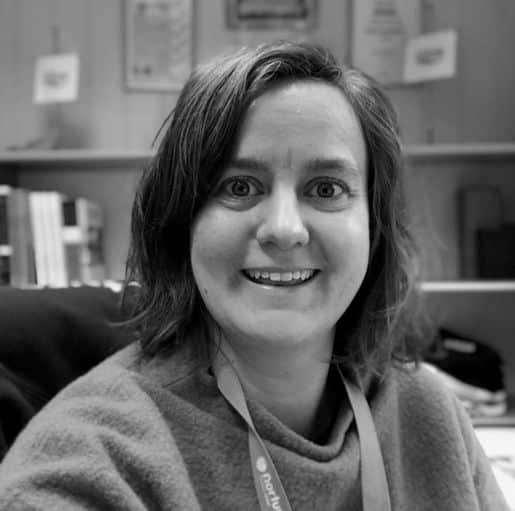
Another important aspect is that more than the cobot itself is needed. There’s simply no use for a cobot without a tool and some customization. Additional hardware and software settings are necessary for a fully functional palletizing solution.
To draw a rough and simplistic comparison – humans use their hands to manipulate objects and need a brain to know how to do it. A tool is required to manipulate objects, and software is necessary to control them effectively. The same goes for cobots.
But a cobot needs more than just a tool.
Hardware for a cobot palletizing solution
You need hardware to have a complete cobot palletizing solution. One of the mandatory hardware peaces is the lifting column or a fixed pedestal and a frame, the gripper tool, and sensors. Additional hardware may also be needed, depending on specific use cases.
Lifting column, fixed pedestal and the frame
The mandatory hardware equipment is a lifting column or a fixed pedestal. This type of hardware basically connects the robot to the ground and adds a bit of needed height to fulfill its task as a palletizing solution.
A lifting column is often necessary, especially with the UR10e, to provide the solution with extra vertical mobility. This is especially true for palletizing projects with larger cases, extending the total pallet height beyond its reach.

Alternatively, a fixed pedestal can also work if the reach is less of an issue. However, this limits your flexibility to adapt to other projects needing extra vertical mobility.
Then there is the frame. The frame serves the purpose of tidying cables neatly within a closed space. It also helps protect the control box and associated hardware from the work environment. This is worth the investment to avoid accidental damage and downtime in production.
Gripper
As an essential part of a palletizing solution, the gripper makes it possible to pick up and place your product with precision.
Recent years have seen advancements in the technology used to pick up products and cases. The most popular grippers today have vacuum technology, making products in many shapes and sizes stick onto its surface.
Three things to consider when choosing a gripper is the Tool Center Point (TCP), the size and its weight.
A well suited gripper for palletizng have a TCP offset which slightly increases the reach of the cobot. This is beneficial in certain scenarios where the pallet pattern requires that extra length to reach all the corners on the pallet pattern.

Increase in the gripper size also increases the possible products it can grip and move in a single cycle. This is beneficial as the solution can be efficient with less and slower movements.
Finally, the weight of the gripper influences its max payload. Therefore, a light gripper is preferable, as it can lift more and heavier products in one cycle.
Sensors
As the robot itself does not have “eyes”, sensors become necessary to give the system information about the external environment. For example, it needs to know when it can pick up new products, as they’re not always be available on the conveyor.
Software for a cobot palletizing solution
For palletizing, there are two software options. The first option is to use free software that provides limited possibilities. The other option is to invest in additional software offering extra palletizing features. This allows you to install and set up a new solution easier while also having the flexibility to adapt to new projects quickly.
It is not to be underestimated that the calibration of a robot program can be complex. This is one of many reasons why the Pally software can be beneficial for palletizing. Below you can see Bjørnar, one of our automation experts, setting up a palletizing project with the two different software options.
Pally palletizing software for UR cobots
Pally URcap is designed to be smooth, flexible and quick to install. To get an efficient and reliable palletizing solution using the UR cobots, Pally is a key component to limit the downtime in production. It is the brain of the operation which gives the operator the features needed to manage the palletizing process with ease.
Having great software also have sustainable benefits. Especially with features like the Smart Grip and Path Planning, the solution will be running optimally from the start. It will be optimized to lower the total cost of operations while increasing the lifetime value and safety.

Contact us to learn more about palletizing solutions with Pally
We see huge potential with Pally and UR20 as many of the benefits with Pally make even more sense with a larger cobot. The ability to smart grip boxes (based on calculations, Pally chooses how many or how few boxes to pick) allows for more safety, higher cycle time, and less strain on the robot. With an increased payload, the possibilities for this are vastly improved. With MyRobot.cloud, you are able to test your project before buying.
Roger Almaas
Customer Service Manager at Rocketfarm
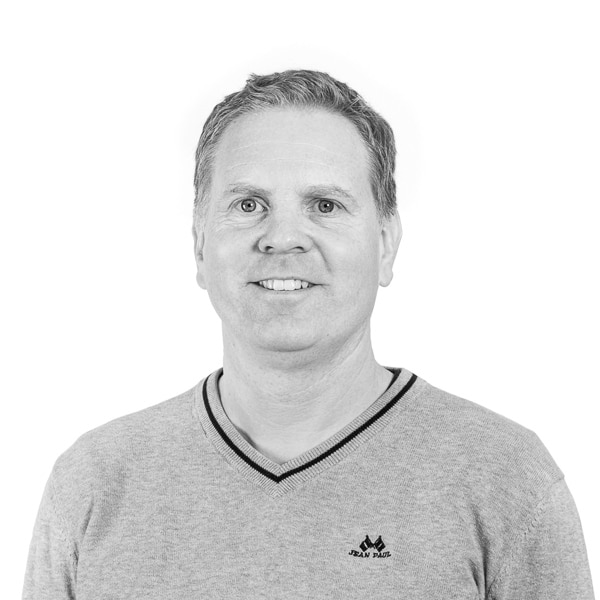
Sales process
Getting a market-leading palletizing solution up and running is a process. Previously, it was a process that would be very time-consuming and costly. Now, on the other hand, this process has changed.
A few years ago, the primary process consisted of lab engineering, sales, Factory Acceptance Test (FAT), Site Acceptance Test (SAT), installation, and training. The processes also depended on component vendors, integrators, and distributors working together to provide a working solution.
Looking back, this could have been more efficient and caused significant bottlenecks in the adoption process.
Today, however, most of these steps have either been shortened or replaced due to emerging digital tools such as MyRobot.cloud.
MyRobot.cloud
MyRobot.cloud helps sales engineers streamline their sales process using Digital Twin simulations of palletizing solutions. Digital Twin technology makes it possible to create accurate digital robots based on the same hardware and software stack as real ones.
With an accurate digital representation of a robot, it can deliver trustworthy and credible evidence about the feasibility of a project. This evidence comes in the form of a video, installation details, and a performance rapport.
This gives the sales engineers the tool to quote their customers more quickly. As pointed out by Parker below, it provides tools that make the sales process easier.

Digital Twin Simulations is a powerful tool and a great benefit to our customers. Verifying projects in real-time makes our quoting and sales process more effective and efficient.
Parker Morris-Pinson
Inside Sales Specialist, Columbia/Okura

Fast Track to Cobot Palletizing solutions
But you don’t need to be a sales engineer to look into different palletizing solutions. The Fast Track to Cobot Palletizing is the world’s first search engine for cobot palletizing solutions. The fast track will simulate and present you with available solutions based on your specific product specifications and production capacity. It will even match you with solution providers in your region!
Summary
When considering a cobot palletizing solution, it is essential to consider the type of robot required, the extra hardware, and the software. While the robot is a vital part of a palletizing solution, other essential components are needed, like the frame, lifting column or pedestal, gripper, and sensors.
In addition to the hardware, palletizing software such as the Pally URcap can make the solution perform better. The Pally software makes installation and daily operations more accessible and provides the functions needed to adapt to new projects faster.
It is also worth noting that selling and buying a solution has recently become much easier and faster. This is because of the emerging digital tools that can quickly present evidence of the solution’s feasibility. The customer also pays for this process, but since the process is more optimized, the total cost is lower than before.
In terms of what you actually pay for, we have in this article talked about the following:
- The robot
- Palletizing hardware
- Palletizing software
- Sales process
In conclusion, the possibility for customization is significant and different customer needs to affect the total cost of a cobot palletizing solution. Ultimately, what you pay for is more than just a cobot. As discussed in this article, the hardware, software, and the process of getting it in your facility are included in the total price tag.
Do you have a palletizing project in mind? Visit the Fast Track to Cobot Palletizing below and verify your project today!
Sign up for our newsletter and get a FREE ebook
By signing up for our monthly newsletter, you’ll get case stories, product launches, and tips to automate your production line!
Additionally, you will instantly receive an ebook about implementing palletizing. For more information, please visit our newsletter subscription page.
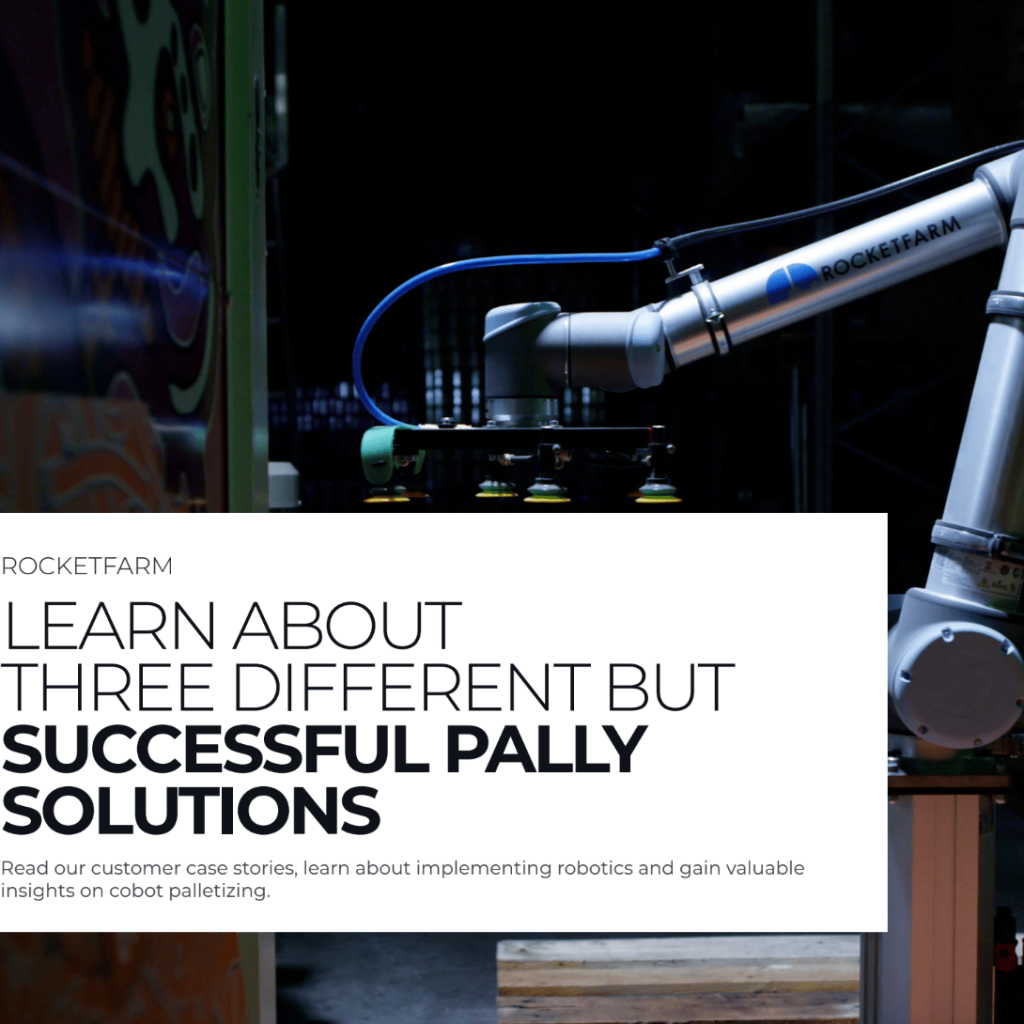